فرآوری محصول خام استخراج شده از معادن سنگ به سنگدانه قابل استفاده در بتن، میتواند فرآیندی بسیار ساده یا وابسته به عوامل متعدد باشد. اما چه عواملی میتواند فرآیند فرآوری را تحتتأثیر قرار دهد؟ و آیا برای تولید و فرآوری باید اقدامات خاصی انجام گیرد؟ در این مقاله از بلاگ رامکا درصدد هستیم تا ضمن پاسخگویی به این سؤال، به بررسی روش تولید و فرآوری سنگدانه بتن بپردازیم. پس تا انتها همراه ما باشید.
مرحله روبارهبرداری
پیش از حفاری، لازم است روباره – که شامل پوشش گیاهی، درختان، خاک زراعتی، رس و… است – را تا رسیدن به مصالح مورد نظر برداشت کنید. اصولاً بین تولید و فرآوری سنگدانه بتن از بستر یا تودههای دانهای در دست بهرهبرداری تفاوتی وجود ندارد. روبارهبرداری باید به گونهای انجام شود که نیاز به جابهجایی مجدد مواد نباشد. بیلهای مکانیکی یا بیلهای کششی کابلدار، اغلب جهت بارگیری کامیونها استفاده قرار میشوند و کامیونها مواد را درون بخشهای استخراج شده گودال معدن روباز تخلیه میکنند.
در تودههای عمیق دارای روباره کم، روبارهبرداری را میتوان قبل از استخراج به صورت متناوب به کمک بولدوزرها انجام داد. در تودههای سطحی با روباره نسبتاً بیشتر، روبارهبرداری حین استخراج ماده معدنی به صورت پیوسته انجام میشود.
در برخی موارد با استفاده از اسکریپرهای تکنفره پیشرو – پسرو دوموتوره چرخ لاستیکی با حجم بارگیری ۱۸٫۵ متر مکعب یا بیشتر، میتوان هزینه تمام شده استخراج را کاهش داد. این ماشینهای چندکاره قادرند مسیرهای حمل خود را نگهداری کرده و در شرایط مناسب با سرعت زیاد حرکت کنند.
تعیین عمق روبارهبرداری اقتصادی بایستی با توجه به اینکه در موارد نادری این عمق جهت دستیابی به مواد دلخواه به بیش از ۱۵ متر بالغ شده است، صورت پذیرد. بعضی کارگاههای تولید شن قادرند بخش فوقانی لایههای رسی را در تولید مصالح اساس استفاده قرار داده و شن تمیز لایههای زیرین را به صورت سنگدانه ساخت بتن استخراج کنند. شکافندههای چرخ زنجیری دارای تیغههای بولدوزری یا بدون تیغه، جهت خرد کردن سنگهای سست یا زمین یخ بسته در عملیات روبارهبرداری استفاده میشوند.
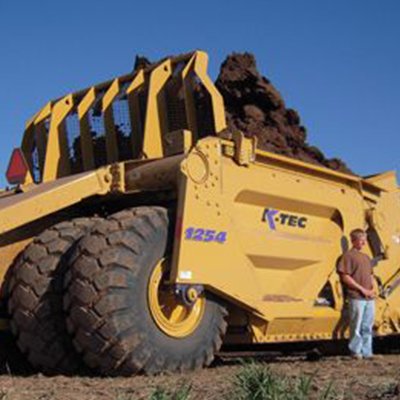
مرحله آتشباری در معادن سنگ
در تولید و فرآوری سنگدانه بتن، بیشتر سنگها در معدن روباز به وسیله آتشباری مواد منفجره به قطعات کوچکتر خرد میشوند تا پس از آن در مراحل سنگشکنی قابل استفاده باشند. فاصله چالها و نوع ماده منفجره، باید با توجه به سختی سنگ معدن انتخاب شود. این امر نیازمند هماهنگی و همکاری نزدیک بین تولیدکننده مواد منفجره و بهرهبرداری معدن است. پیشرفت سریع تکنیکهای حفاری و خصوصیات مواد منفجره، مانع از تدوین ضوابط و دستورالعملهای دقیق میگردد، اما توجه به نکات کلی زیر مناسب به نظر میرسد:
- انرژی انفجار تنها از انسباط سریع گازهای تحت فشار نشأت میگیرد، لذا چنانچه در ابتدا خرج در انتهای چال قرار گیرد و انفجار به سمت لایههای فوقانی گسترش یابد، نتیجه بهتری حاصل میشود. همچنین استفاده از مواد منفجره قویتر در ته چال نیز نتایج مشابهی را به همراه خواهد داشت.
- حفر چالهایی با قطر کمتر و فواصل نزدیکتر به فاصله معینی عقبتر از سینه کار یا لایه فوقانی، موجب دستیابی به بهترین نتیجه میشود. همچنین میتوان با حفر چالهایی در ردیفهای غیرمتوالی (یک در میان) و انفجار با استفاده از چاشنیهای تأخیری مواد را بیشتر خرد نمود.
- در سنگهای سختتر، چالها بایستی در فواصل نزدیکتر حفر گردند.
- هر چه ارتفاع سینه کار بیشتر باشد، میتوان چالها را با فاصله بیشتری حفر نمود. فواصل حدود ۳ متر تا ۹ متر متداول است.
- چالهای انفجار را با روشهای حفاری کابلی، ضربهای، چرخشی و با روش حرارتی ایجاد میکنند. در حفر چال، میله کوبنده متناوباً بالا و پایین میرود و با ضربهزدن روی میله فولادی حفاری انجام میگیرد. نوک میله فولادی از تیغههای تیز پوشیده شده است. بدیهی است استفاده از این روش فقط در چالهای قائم امکانپذیر است. در حفاری ضربهای از مته فولادی کربورگذاری شده، استفاده میشود و برای خارج کردن قطعات خرد شده ته چال از هوای فشرده استفاده میگردد. حفاری چرخشی معمولاً در سنگهای سست استفاده میشود. چنانچه در حفاری ضربهای و چرخشی دکل مناسبی به کار گرفته شود، میتوان در زوایای دلخواه درون سنگ حفاری نمود.
- در تولید و فرآوری سنگدانه بتن، انواع گوناگون دکلهای حفاری موجودند که معمولاً چرخ زنجیری با بازوی هیدرولیکی دارند و جهت کنترل دقیق میله و سر مته حفاری مناسب هستند. قطر چالهای حفاری حدود ۱۰۰ تا ۲۰۰ میلیمتر است. در حفاری با روش حرارتی از گرمای شدید ناشی از اختلاط نفت خام و اکسیژن، جهت گداختن و خرد کردن سنگ استفاده میشود. به منظور بهبود فرآیند خرد کردن و خارج نمودن خرده سنگها از چال، از بخار استفاده میشود.
- انواع مختلف مواد منفجره جهت انفجار سنگها در دسترس هستند. موارد کاربرد مواد منفجره بسته به مقاومت، میزان انفجار، طرز قرار گرفتن آنها درون چال و حساسیت مواد منفجره متفاوت است.
در مجموع عملیات آتشباری برای مدیران استخراج، فرآیندی پیچیده و تخصصی است و تصمیمگیری بایستی با رعایت متغیرهای زیر صورت پذیرد:
- ارتفاع سینه کار
- سختی و یکنواختی سنگ
- شیب طبقات
- نحوه توزیع شکافها و درزهای طبقات
- شیب سکوهای معدن
- اندازه و عمق چالهای حفاری
- فاصله و آرایش چالهای حفاری
- تعداد چالهایی که در یک لحظه منفجر میشوند
- میزان خرج
- موقعیت خرجهای درون چالها
- نوع ماده منفجره مورد استفاده
- روش آتش کردن
- نحوه بارگیری سنگ
- ظرفیت بیلهای بارگیری
- اندازه سنگشکنها
مرحله استخراج و تولید سنگدانه بتن
تولید و فرآوری سنگدانه بتن با بیل مکانیکی
سنگهای شکسته شده ناشی از آتشباری سینهکار معدن، معمولاً به وسیله بیلهای مکانیکی با جام به ظرفیت بین ۰٫۷۵ مترمکعب تا۷٫۵ متر مکعب برداشته میشوند. بیلهای مکانیکی الکتریکی با جامهای ظرفیت بالا جایگاه مناسبی کسب کردهاند و جریان الکتریسته از طریق کابلهای انعطافپذیر فراهم میشود. طبق آمارهای موجود در روش تولید و فرآوری سنگدانه بتن، بیلهای مکانیکی جهت بارگیری هر تن سنگ، تنها ۰٫۲۲kWh برق مصرف میکنند.
این جریان متناوب با ولتاژ بالا به بیل وارد شده و مبدلهای ac/dc، موتورهای dc را برای فرآیندهای مجزا به کار میاندازند. پیشرفت عملیات بارگیری سنگ به کمک جام ۱٫۸ مترمکعب با زاویه دوران ۹۰ درجه در حدود ۱۴۵m3/hتا ۲۰۰m3/h گزارش شده است. با استفاده از جامهای بزرگتر، میزان بارگیری به همین نسبت افزایش نمییابد، اما نیروی خیلی بیشتری دارند و در صورت لزوم به کار میروند.
رسوبات شن و ماسه با لایههای فوقانی نسبتاً کم ضخامت، با استفاده از بیلهای مکانیکی استخراج میشوند. میزان بارگیری بسیار فراتر از آنچه در بالا برای سنگ قید شده است و با جام به ظرفیت ۱٫۸ متر مکعب حتی میتوان ۲۹۰m3/h مواد شنی سست را بارگیری و حمل نمود. در سینه کارهای بلندتر به دلیل خطر ریزش و مدفون شدن، بیل مکانیکی کاربردی ندارد. لذا در این موارد از بیلهای کششی کابلی استفاده میشود.
تولید و فرآوری سنگدانه بتن با بیل کششی کابلی
امروزه بیلهای کششی کابلی با بازوهای بلندتر و جامهای بارگیر بزرگتر موجودند و بازوهای به طول ۳۶ متر و جامهای ۱۱ متر مکعب غیرمعمول نیست. تعدادی از بهرهبرادران بار کردن مواد را از بالا و برخی دیگر بار کردن مواد را از پایین مناسب میدانند.
بار کردن توده به سمت پایین برای فرآیند استخراج کاملاً خشک است که متصدی دستگاه به مخلوطی از مواد و توده دستنخورده با هر یک از مواد مورد نظر دسترسی دارد. چنانچه بخشی از سینهکار زیر آب باشد، بارگیری مواد به سمت بالا اجباری است. در این روش، احتمال فرو رفتن ماشین هنگام بالا کشیدن توده در اثر آبشستگی وجود دارد.
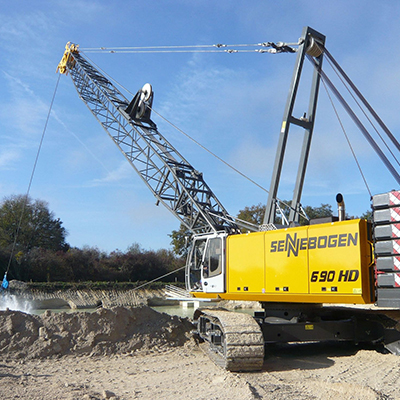
برد بیلهای کششی را با استفاده از سیستمهای کابل هوایی و با بکارگیری وزنه مهار میتوان به میزان زیادی افزایش داد. در این روش، جام قرقرهای خراشنده به وسیله کابل به تکیهگاه ثابتی در فاصله نسبتاً دور متصل است و در سطوح پایینتر نسبت به ماشین کار میکند.
برای برداشتن هر لقمه، کابل محکم شده و جام در اثر نیروی وزن به فاصله معینی پایین راننده میشود. سپس کابل نگهدارنده سست شده و جام به سمت پایین توده میافتد. کابل بارگیری مجزا که مستقیماً به جام متصل شده است، آن را به طرف ماشین میکشد تا بارگیری شود. در حفر چندین ترانشه عمیق، یافتن وضعیت جدید وزن مهار ضروری است تا اینکه ماشین بتواند به صورت شعاعی حول وزنه مهار حرکت نماید.
با استفاده از کابل دیگر با قرقره شیاردار در تراز وزنه مهار میتوان مواد را به سمت بالا یا حتی در صورت نیاز به سمت وزنه حفاری نمود. در روش کابل هوایی تنوع زیادی در نحوه بارگیری یا تشکیل تودههای موجدار وجود دارد و فواصل قابل توجه قائم و افقی را میتوان تحت پوشش قرار داد.
استخراج هیدرولیکی سنگدانه بتن
عملیات لایروبی در رسوبات زیرآبی اغلب به سادگی انجامپذیر است. تجهیزات لایروبی روی یک شناور یا کشتی نصب شده و مواد برداشت شده اغلب جهت فرآوری به ساحل پمپاژ میشود یا در بعضی موارد، شناورهای مجاور که دارای تجهیزات فرآوری هستند، این عملیات را انجام میدهند. مکش توسط پمپهای گریز از مرکز ایجاد میشود که لولههای آن در برابر سایش به وسیله آستر به طرز خاصی تقویت شدهاند و معمولاً به وسیله موتورهای ۲۰۰hp یا حتی خیلی بزرگتر کار میکنند.
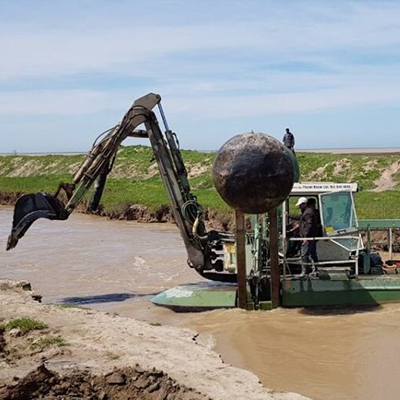
لوله مکش که قطر آن بین ۲۰۰ تا ۷۰۰ میلیمتر متغیر است، به کمک قاب دارای آرایش A شکل به وسیله جرثقیل کابلی و بالابر تا کف رسوبات پایین برده میشود. اغلب در رسوبات ماسهای نرم، ایجاد مکش به تنهایی برای بالا آوردن مواد کافی است، اما در رسوبات سختتر حاوی شن بایستی برای خارج کردن مواد از ابزارهای مکانیکی استفاده نمود.
این قبیل ابزارهای مکانیکی شامل انواع مختلف خردکنندههای چرخشی یا نردبانهای زنجیری استخراج با ساختار ویژه است که بر سر لوله نصب میشوند تا از گرفتگی لوله مکش به وسیله قطعات درشت جلوگیری کنند. مقادیر فراوانی آب همزمان با مواد دانهای پمپ میشود که مواد ریزدانه مورد نیاز بتن را میشوید.
به منظور انجام عملیات حفاری خشک در روش تولید و فرآوری سنگدانه بتن، میتوان بندهای خاکی را احداث کرد و آب ساکن پشت آن را خارج نمود. بیلهای منقاری و جامدار روی شناور نیز جهت استخراج مصالح زیرآبی مورد استفاده قرار میگیرند.
بیشتر بخوانید: سنگدانه بتن
مرحله جابهجایی مصالح
فرآیند تولید و استخراج سنگدانه به نوعی با عملیات حجیمی همراه است که نیازمند جابهجایی این مقادیر زیاد در فواصل نسبتاً طولانی، حتی داخل محوطه کارگاه است. هر متر مکعب سنگدانه، تقریباً ۲ تن (بیش از ۲٫۷ تن در مورد سنگ بستر سنگین) وزن دارد و تلاش مدوامی برای یافتن روشهای اقتصادیتر جابهجایی این تناژ بالا صورت میپذیرد.
کارخانهها از انواع مختلف ماشینآلات جهت جابهجایی مواد استفاده میکنند که شامل خطوط راهآهن، خطوط واگن برقی، کامیونها، شناورها و نوار نقالهها است. دیگران تقریباً برای همه فرآیندها از نوار نقالهها بهره میبرند.
فرآوری سنگدانه بتن با خطوط راهآهن
در عملیات معدنکاری و استخراج سنگ به ویژه هنگامی که مسیر حمل به کارخانه بیش از ۱٫۶ کیلومتر باشد، از لوکوموتیوهای دیزلی-الکتریکی با انواع مختلف واگنها استفاده میشود. هر چه فاصله محل استخراج از کارخانه بیشتر شود، میتوان ریلهای اضافی نصب نمود.
این روش علیرغم نصب ریلهای اضافی و تعمیر و نگهداری آنها اقتصادیتر به نظر میرسد. با استفاده از انواع مختلف واگنهای تخلیهشونده جانبی، تخلیه سریع بار در کارخانه امکانپذیر است، اما از واگنهای تخلیهکننده تحتانی نیز استفاده میشود. ظرفیت واگنها به ۵۰ تن میرسد و در خطوط ریلی کمعرض از واگنهای بسیار کوچکتر نیز استفاده میشود.
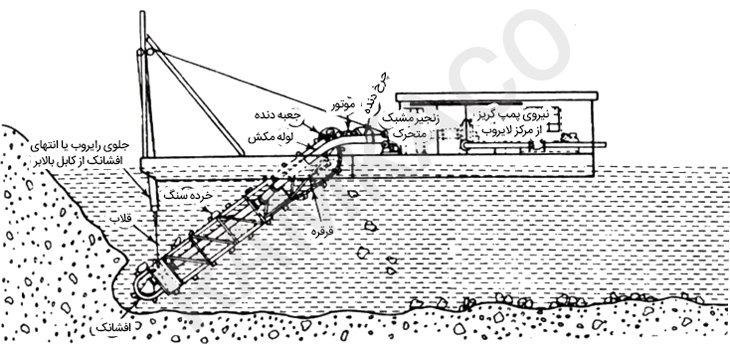
فرآوری سنگدانه با کامیونها
اندازه و شکل جام کامیونها بسیار متنوع است و ظرفیت آنها بدون یدککش به ۸۵ تن بار غنی میرسد. به لحاظ قدرت مانور کامیونهای بدون یدککش، استفاده از آنها جهت جابهجایی درون کارگاه رایج شده است.
همچنین محدودیتهای حملونقل بزرگراههای عمومی نیز وجود دارند و جابهجایی مواد تا حدی که مسیرهای حمل کارخانه را بتوان در شرایط خوب نگهداری کرد، اقتصادی به نظر میرسد. بسیاری از بهرهبرادران بر شرایط مسیرهای حمل به لحاظ آسیبهای وارده به چرخهای لاستیکی بزرگ کامیونها تأکید فراوان دارند.
نگهداری بسیار خوب مسیرهای حمل، موجب کاهش میزان خستگی راننده و هزینههای تعمیر و نگهداری نیز میشود. در بعضی کارخانهها، گریدر تیغهای هموار کردن مدوام مسیرها و زدودن سنگهای پراکنده را بر عهده دارد. در این میان، گاهی اوقات جامهای تخلیهشونده جانبی استفاده میشوند، اما استفاده از انواع تخلیهشونده انتهایی احتمالاً به دلیل پایداری واقعی یا فرضی بیشتر آنها متداول است.
فرآوری سنگدانه با نوار نقاله
مصالح تقریباً همیشه توسط نوار نقالهها حمل میشوند. نوار نقالهها میتوانند به راحتی مصالح را به سمت بالا، پایین یا به صورت افقی حمل نمایند، اما معمولاً شیب آن نسبت به افق نباید از ۲۰ درجه تجاوز کند. زوایای بیشتر موجب غلتیدن سنگهای بزرگ به پایین نوار نقاله میشود.
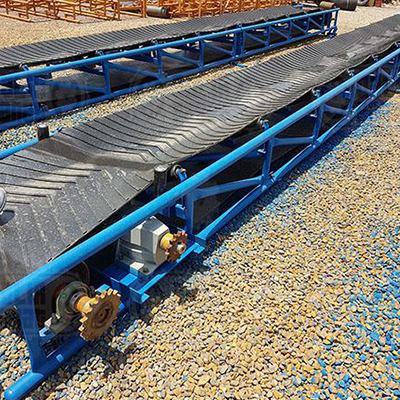
حمل مواد خام استخراجی از معدن روباز سنگ به لحاظ وارد آمدن آسیب احتمالی به تسمه نوار نقاله توصیه نمیشود، مگر اینکه در ابتدا اندازههای بزرگ جدا شوند؛ بدین منظور بایستی سرند کردن و سنگشکنی اولیه در نزدیکی محل استخراج انجام گیرد.
نوار نقالهها در مواردی نظیر توده کردن مصالح، بارگیری واگنها، سیلوها و کامیونها و تشکیل تودههای موجدار مورد استفاده قرار میگیرند. گاهی اوقات تسمهها در مرکز نوار بارگیری شده و با معکوس کردن جهت حرکت تسمه، مواد در هر یک از دو انتهای نوار توده میشوند. نوارهای کوتاه (تا حدود ۱۸ متر) روی چرخ سوار شده و به منظور بارگیری، به سرعت به نقاط مختلف کارگاه منتقل میشوند. البته ابزاری برای توزین بار عبوری از نوار نقاله در فاصله زمانی معین وجود دارد که از سیستمهای توزین متداول به همراه جمعزنهای ویژه استفاده میکنند. همچنین اخیراً روشی بر اساس اصول اندازهگیری هستهای در روش تولید و فرآوری سنگدانه بتن به کار میرود.
مرحله سنگشکنی
عملاً تمامی سنگهای استخراج شده روباره و اندازههای بزرگ در معدن بایستی به اندازههای قابل استفاده در بتن خرد شوند. چنین خرد کردنی به وسیله انواع مختلفی از ماشینآلات سنگشکنی ساخته شده انجام میشود که انواع آن به صورت ذیل طبقهبندی میشوند:
- فکی
- ژیراتوری یا مخروطی
- استوانهای- غلتکی (یکغلتکی، دوغلتکی یا سهغلتکی)
- چکشی
- ضربهای
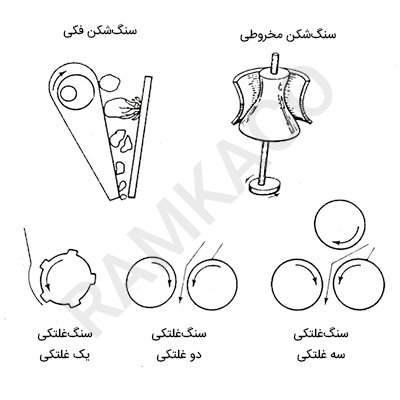
جهت انتخاب نوع سنگشکن مناسب برای کاربری خاص، بایستی به موارد زیر توجه نمود:
- طرح و اندازه سنگشکن باید به گونهای باشد که بزرگترین اندازه مواد ورودی را خرد کند.
- ظرفیت سنگشکن باید چنان باشد که قادر به خرد کردن حداکثر نرخ بار ورودی باشد.
- وجود ذرات ریز در بار ورودی، نباید باعث گیر کردن و کاهش سرعت سنگشکن گردد.
- قطعاتی که قابلیت فرسایش دارند، بایستی روکشی داشته باشند که به آسانی تعویض شود.
- بایستی تمهیداتی جهت آهن یا سایر مواد غیرقابل خردشدن که گهگاه داخل بار ورودی میشوند، اندیشید. به دلیل ورود چنین موادی نباید به سنگشکن آسیبی برسد، ولی گاهی افت سرعت (راندامان) و گیر کردن غیرقابل اجتناب است.
با گذشت دوران، تلاش زیادی روی سنگشکنها صرف شده تا خصوصیات محصول ارزیابی گردد؛ یعنی تعیین شود که آیا سنگها به نوعی به قطعات دراز و ریز یا قطعات مکعبی و بلوکی میشکنند. قطعات خردشده مکعبی یا بلوکی برای استفاده در بتن مناسبتر هستند، زیرا میزان تخلخل آنها کمتر بوده و ملات ماسه، سیمان و آب کمتری نیاز دارند.
عموم متخصصین بر این عقیدهاند که سنگشکنهایی برای شکستن سنگ از ضربه زدن استفاده میکنند، مانند سنگشکنهای چکشی یا ضربهای و در برابر آن، بعضی سنگشکنها از فشار برای خرد کردن بهره میبرند، نظیر فکی یا استوانهای دوغلتکی. در این میان دومین نوع سنگشکنها، محصول مکعبیتری را فراهم میکنند.
در عین حال، سنگهای ورقهای نازک در امتداد لایهها میشکنند و این امر به نوع سنگشکن مرتبط نیست، اما کارایی سنگشکن بایستی با توجه به خصوصیات سنگ معین ارزیابی شود. سنگشکنهای ژیراتوری به نسبت مساوی از فشار و ضربه جهت خرد کردن استفاده میکنند و شاید به همین دلیل است که در صنایع تولید و فرآوری سنگدانه بتن استفاده میشوند.
سنگشکنهای فکی به صورت گسترده در خرد کردن اولیه قطعات سنگ بستر به کار میروند که این امر ناشی از بازشدگی زیاد فک آنها تا میزان ۱۶۵۰mm*2150mm است. پوششهای مخصوص فک فولادی قابل تعویض بوده و به صورت منحنی، صاف یا موجدار به کار میروند و با استفاده از انواع سنگشکنهای مختلف، میتوان انواع حرکتهای فک را ایجاد نمود.
در سنگشکن فکی معمولی، فک خارج از مرکز نصب شده است که جابهجایی ورودی فوقانی نسبت به جابهجایی اندک خروجی انتهایی، بسیار بزرگتر است. کلیه سنگشکنهای فکی از چرخ لنگر بزرگی استفاده میکنند تا انرژی برای ضربات بعدی ذخیره شود. اعتقاد بر این است که اگر خرد کردن بیش از حد بار ورودی در یک مرحله سنگشکنی مد نظر نباشد، سنگشکنهای فکی، ریزدانه کمتری نسبت به سایر انواع سنگشکنها تولید میکنند.
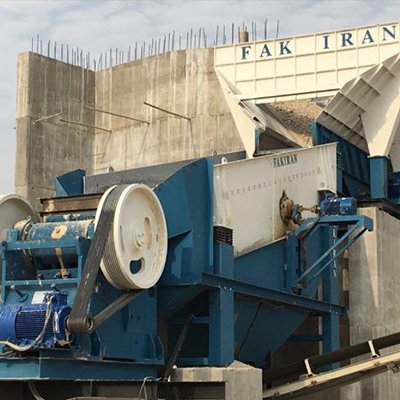
سنگشکنهای ژیراتوری مورد استفاده در در روش تولید و فرآوری سنگدانه بتن، شامل یک میله قائم هستند که مخروط یا کلاهک را حمل میکند. مخروط نمیچرخد، اما حرکت چرخشی خارج از محور به وسیله انتهای میله وارد میشود. از این رو بیشترین جابهجایی مخروط در خروجی تحتانی و کمترین جابهجایی در قسمت فوقانی استباشد. مخروط درون کاسه مخروطی شکل میچرخد و لذا فاصله بین مخروط و کاسه همیشه گوهای شکل است.
این روش خرد کردن تا حدودی شبیه عمل سنگشکن فکی است، با این تفاوت که انحنای مخروط و کاسه، تنشهای برشی و خمشی به سنگ وارد میکند. سنگ در بین دو بازشدگی نیمدایرهای شکل در بالای سنگشکن قرار دارد، اما به دلیل استقرار میله و قابهای نگهدارنده، حداکثر اندازه سنگ به ۱۸۰۰mm محدود میشود.
سنگشکن استوانهای (غلتکی) که انواع مختلف آن موجود است، به سه دسته تکغلتکی، دوغلتکی و سهغلتکی تقسیم میگردد. سنگشکن تکغلتکی دارای استوانه است که غلتک سختکوب نیز نامیده میشود. این سنگشکنها گاهی به عنوان سنگشکن اولیه مورد استفاده قرار میگیرند.
استفاده از سنگشکنهای غلتکی در روش تولید و فرآوری سنگدانه بتن چندان متداول نیست، اما جهت شکستن و خرد کردن سنگدانه به اندازههای ریز در یک بار سنگشکنی مفید هستند. امکان استفاده از این سنگشکن به منظور فرآوری سنگ مورد نیاز مصارف کشاورزی یا تولید سیمان پرتلند وجود دارد.
خرد کردن سنگدانه مورد نیاز بتن همواره به صورت مرحلهای انجام میشود، یعنی پس از سنگشکنی اولیه، دانههای کوچکتر دارای اندازه مطلوب جداشده و دانههای بزرگتر مجدداً توسط سنگشکن ثانویه خرد میشوند. کاهش اندازه دانهها در سنگشکن غلتکی، معمولاً از حدود ۱:۴ جهت تولید حداقل ریزدانهها تجاوز نمیکند.
بیشتر بخوانید: معادن سنگدانه بتن
مرحله سرند کردن
سنگدانههای مورد استفاده در بتن بایستی دارای اندازه دانههای مناسب باشند و این امر نیازمند سرند کردن محصول جهت دستیابی به اندازههای مورد نیاز است. به استثنای جدا کردن ماسه از مواد اولیه توده شده، در روش تولید و فرآوری سنگدانه بتن واژه سرند کردن منحصراً به تهیه درشتدانهها، یعنی دانههای بزرگتر از الک نمره ۱۰ (۲mm) اطلاق میگردد.
جداسازی ذرات درشت سنگدانه به وسیله انواع گوناگون سرندها که دارای چشمههای مربعی، گرد، لوزی شکل یا مستطیلی هستند، انجام میپذیرد. مصالح به اندازه ماسه، تقریباً به طور کامل توسط ابزارهای طبقهبندیکننده هیدرولیکی فراهم میشوند، زیرا جداسازی این مواد بدین روش ساده است. دانهبندی مواد ریزدانه با استفاده از سرندها به کارهای آزمایشگاهی محدود میگردد. نکات عمومی زیر جهت عملیات سرند کردن قابل ذکر هستند:
- بایستی به هر ذره عبوری از سرند که به اندازه کافی کوچک است، فرصت عبور داده شود. به ذرات با شکل نامنظم، بایستی فرصتهای متعددی برای عبور از سرند در جهت کمترین بُعدشان داده شود.
- چنانچه سرند شدیداً لرزانده شود یا شیب آن خیلی زیاد باشد (بخصوص اگر بار سرند نیز کم باشد)، ذرات به جای عبور از سرند روی آن بالا و پایین میپرند، در حالیکه غلتیدن ذرات مورد نظر است.
- اگر بار سرند بیش از حد باشد و به اندازه کافی نیز لرزانده نشود، سرند کور خواهد شد؛ یعنی چشمههای آن با ذراتی که اندکی بزرگتر از آن هستند که عبور کنند، مسدود میگردند.
- سرند کردن دانههای شن کروی، سادهتر از سنگ یا روباره شکسته تیزگوشه است.
- نرخ سرند کردن (بر حسب تن در ساعت) مصالح حاوی دانههایی با اندازههای کاملاً متفاوت بیشتر است. سرند کردن مصالحی که ۹۰% آن عبور میکند، بسیار آسانتر از سرند کردن مصالحی با دانهبندی پیوستهای است که تنها ۱۰% ذرات بگذرند.
- مصالح مرطوب، بخصوص شن ریز راحتتر از مصالح خشک سرند میشوند، اما در صنایع تولید روباره و سنگ شکسته، اغلب اوقات سرند کردن به روش خشک انجام میشود.
تولید و فرآوری سنگدانه بتن با گریزلی (سرند میلهای)
در در روش تولید و فرآوری سنگدانه بتن، مواد خام استخراج شده از معدن سنگ روباز، معمولاً به سرند گریزلی وارد میشوند. این سرند از میلههای موازی تشکیل شده و فاصله بین آنها به گونهای تنظیم میشود که بزرگترین اندازه سنگی که مستقیماً خوراک کارخانه فرآوری را تأمین میکند، عبور دهد. بخش مانده روی سرند، توسط سنگشکن تا اندازه مورد نظر خرد میشود. بسته به خواص بار ورودی، میلههای سرند ثابت یا لرزان هستند.
چنانچه خواص بار ورودی به آسانی و بدون گیر کردن یا آویزان ماندن بین میلهها عبور کند، نیازی به لرزاندن نیست. گریزلیهای شیبدار ارزان، همانند تغذیهکنندههای مکانیکی موجود در بازار عمل کرده و مصالح را به صورت یکنواخت پایین میآورند و روی تسمه، سنگشکن یا سرند پخش میکنند.
برخی گریزلیهای معدن شن، درجا ساخته میشوند و تنها شامل قیفی هستند که شبکه افقی از ریلهای راهآهن روی آن قرار میگیرد تا از عبور دانههای بزرگ یا کلوخهها جلوگیری کند. در صورت نیاز، کلوخهها با پتک خرد میشوند و چنانچه مقدار قلوهسنگهای درشت کم باشد، میتوان آنها را دور ریخت.
متصدیان تولید شن و ماسه، گاهی اوقات مواد خام را به وسیله کامیون یا بیل مکانیکی مستقیماً روی گریزلی ثابت میریزند که مصالح به تدریج بالا آمده و توده موجداری تشکیل میشود. نوار نقالهها، کامیونها و… مصالح را از پایین شیبدار زیر گریزلی حمل میکنند. بایستی دقت شود سرند گریزلی مانع از مسدود شدن دریچه تخلیه سیلو گردد.
تولید و فرآوری سنگدانه بتن با سرندهای گردان
سرندهای چرخشی یا گردان، شامل استوانههای سیمی یا صفحه سوراخدار با انتهای باز هستند که حول محوری با شیب اندک میچرخند. مصالح درون انتهای فوقانی استوانه ریخته میشود و اگر دانهها به اندازه کافی کوچک باشند، حین غلتیدن به سمت پایین (در اثر چرخیدن سرند)، از بین چشمههای سرند عبور میکنند.
دانههای درشتی که از سرند عبور نکنند، از انتهای استوانه درون ناوهای میریزند و پس از خرد شدن، مجدداً سرند میشوند؛ به عنوان مثال با قرار دادن سه سرند استوانهای به صورت هم مرکز که به ترتیب ریزتر میشوند، میتوان چهار اندازه مختلف از مصالح را تهیه نمود که عبارتند از: اندازههای درشتتر از سرند داخلی، مصالح مانده روی دو سرند دیگر و مصالح عبوری از سرند خارجی.
سرند کردن مصالح خشک که با سایش آنها همراه است، موجب تولید گرد و غبار میگردد که آبپاشی برای رفع این مشکل توصیه میشود. در بعضی دستگاههای دیگر که بار ورودی حاوی دانههایی با پوشش رس چسبنده است، مقادیر بیشتری آب توسط افشانکها درون سرند داخلی پاشیده میشود و عملیات شستوشوی دانهها همزمان با سرند کردن آنها انجام میشود.
سرندهای گردان را میتوان در نقاط مختلف چرخه تولید مصالح در کارخانه استفاده نمود. به عنوان نمونه، گاهی اوقات در عملیات تولید شن و ماسه بلافاصله پس از حذف ماسه توسط سرندهای لرزان یا در عملیات معدنکاری بلافاصله پیش از سنگشکن اولیه به منظر جداسازی ذرات درشتی که از گریزلی عبور کردهاند، مورد استفاده قرار میگیرد.
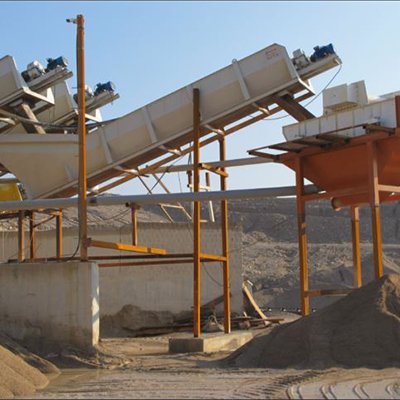
تولید و فرآوری سنگدانه بتن با سرندهای تخت
در در روش تولید و فرآوری سنگدانه بتن، سرندهای ارزان تخت به نحو گستردهای، چه به صورت منفرد یا روی هم چیده شده تا سه سرند جهت تولید مصالح به اندازهای نزدیک به هم مورد استفاده قرار میگیرند. سازندگان مختلف، سرندها را به وسیله وزنههای گردان خارج از محور یا نامتعادل میلرزانند. میتوان وزنهها را طوری قرار داد که حتی وقتی سرند شیب ندارد، مصالح از یک سو به سوی دیگر به سمت جلو حرکت کنند. اکثر سرندها شیب اندکی دارند (معمولاً حدود ۲۰ درجه) که موجب حرکت مصالح تحت وزنشان میشود.
در موارد خاص برای تولید مصالح ریزدانه از سرندهایی با شیب ۴۵ درجه نیز استفاده شده است. به منظور جذب نوسانات سرندها، آنها را روی فنرهای فولادی یا بالشتکهای هوا نصب میکنند. سرندهایی با مساحت گوناگون وجود دارند که ابعاد آنها تا عرض حدود ۱٫۸m و طول ۶m متغیر است.
سرند میتواند سیمی، میلهای یا صفحه سوراخدار باشد. در اغلب سرندهای سیمی، سختکنندههای پشتیبان مانع از فرو رفتن سرندها میشوند. همچنین استفاده از صفحه سوراخدار با چشمههای ۵۰mm جهت نگهداری سرندهای سیمی ظریفتر توصیه میشود.
محاسبه ظرفیت سرند تخت (تن در ساعت) بسته به مجهولاتی است که ارزیابی آنها مشکل است. برخی سازندگان پیشنهاد میکنند ظرفیت سرند بر اساس ظرفیت پایه (تن در ساعت) برای هر متر مربع سرند که به آن ضریب تصحیح اعمال میشود، محاسبه گردد. مقدار ضریب تصحیح برابر حاصلضرب چهار ضریب زیر است:
- تعداد سرندهای روی سرند مورد نظر
- درصد بار ورودی کوچکتر از نصف چشمههای سرند
- آبپاشی مستقیم روی سرند یا عدم انجام آن
- درصد دانههای بزرگ مانده روی سرند
مقادیر این چهار ضریب بر اساس اصول زیر تعیین میگردند:
- بازدهی سرندهای زیرین، اندکی کمتر از سرند فوقانی است.
- هنگامی که درصد دانههای کوچکتر از نصف چشمههای سرند از ۱۰% به ۶۰% افزایش مییابد، ظرفیت سرند با ضریب ۳ افزایش پیدا میکند.
- آبپاشی روی سرندها، ظرفیت سرند کردن را افزایش میدهد؛ مثلاً ظرفیت سرند با چشمههای ۵mm حدود سه برابر سرند با چشمههای ۲۵mm افزایش پیدا میکند.
- ظرفیت سرند در حالتی که مانده روی سرند ۹۰% باشد، در مقایسه با وقتی که ۲۰% است، نصف میشود.
مرحله شستوشو و تولید ماسه
به طور کلی، روش تولید و فرآوری سنگدانه بتن با مصرف مقادیر زیادی آب همراه است. هدف استفاده از آب میتواند یک یا چند مورد از موارد زیر باشد:
- زدودن اندود چسبنده نامطلوب، نظیر رس، سیلت یا گرد سنگ
- لغزنده کردن سنگها جهت تسریع فرآیند سرند کردن
- کاهش گرد و غبار ناشی از سرند کردن به روش خشک یا سنگشکنی یا جابهجایی مصالح
- دانهبندی یا طبقهبندی آبی ماسه
عملیات سنگشکنی و سرند کردن روباره یا سنگ بسیار سخت نظیر کوارتز، جدا از آبپاشی اندک جهت کنترل گرد و غبار، به صورت کاملاً خشک انجام میشود. در چنین مواردی اغلب مواد ترکننده ویژهای جهت افزایش کارآیی به آب افزوده میشود. استفاده از مقدار اندکی آب تصفیه شده برای جلوگیری از گلوله یا کلوخه شدن مصالح به ویژه هنگامی که ماسه شکسته با عملیات سنگشکنی به وسیله آسیای غلتکی یا تغاری خرد میشود، مطلوب به نظر میرسد.
شستوشوی سنگدانهها به دو روش خیس کردن آنها به صورت کامل با آب تحت فشار به وسیله میلههای افشاننده با افشانکهایی که بالای سرند تخت یا درون سرندهای گردان آویزان میشوند یا غرقاب کردن کامل و سایش شدید به وسیله شویندههای الواری یا سایندههای آبی انجام میشود. روش شستوشو با توجه به چسبندگی پوششی که باید زدوده شود و دیگر مشخصات سنگدانهها تعیین میگردد.
به علاوه در بسیاری از فرآیندهای تولید شن و ماسه از هر دو روش بهره گرفته میشود، مثلاً تنها برای شستوشوی درشتدانهها از میلههای افشاننده طی سرند کردن اولیه و سپس شستوشو با شویندههای الواری استفاده میشود.
شویندههای الواری و سایندههای آبی
هنگامی که اندود رسی چسبیده به سنگدانه به گونهای است که نیازی به عملیات شستوشوی کامل توسط شویندههای الواری وجود ندارد، از سایندههای آبی استفاده میشود. این سایندهها شامل مخازن استوانهای هستند که رو به محوری افقی یا با شیب کم میگردند و سنگدانه همراه با مقدار زیادی آب از یک طرف درون آن ریخته میشود.
بالابرندههایی که درون مخزن استوانهای نصب شدهاند، سنگدانه را بالا برده و در هر دور، درون آب فرو میریزند و مصالح را به شدت به هم میزنند. ذرات ریز معلق به وسیله آب شسته میشوند. دستگاههای مرکب سرندکن – شوینده که سنگدانه را در حالت تَر سرند میکنند، شامل سرند داخلی استوانهای شکل، هم مرکز با پوشش محکم خارجی هستند که همزمان با شستوشو، عمل جداسازی سنگدانههای ریز و درشت را انجام میدهند.
در شویندهها پرههایی جلوی جریان آب عبوری قرار دارند که موجب شستوشوی کاملتر نسبت به حالتی میگردند که تنها از سرند کردن گردان مرطوب استفاده میشود.
نام شویندههای الواری از عملیاتی قدیمی که در آن مخلوط آب و سنگدانه همراه با الوارهای چوبی جهت شستوشوی بهتر درون استوانه گردان ریخته میشد، سرچشمه میگیرد. قلوهسنگهای بزرگ بادوام نیز به همین منظور استفاده میشدند که دستگاهی مشابه آسیای گلولهای بوده است. امروزه شویندههای الواری که بسیار شبیه آسیاهای میلهای هستند، شامل محفظه اندکی مایل هستند که سنگدانه همراه با مقدار زیادی آب از دهانه تحتانی درون آن وارد میشود.
پیچها یا محورهای چرخنده با همان شیب، تیغههای فولادی سخت را حرکت میدهند که این عمل مصالح را به شدت به هم میزند و جهت تخلیه به سمت دهانه فوقانی میراند. اندودهای چسبنده به کلی از روی سطح سنگدانه زدوده شده و عمل سایش برای از هم پاشیدن قطعات نرمتر نظیر ماسهسنگهای نرم، خاک سرخ و شیل نرم کافی است. رس معلق و گرد سنگ حاصل از سایش نیز همراه آب دفع میشوند.
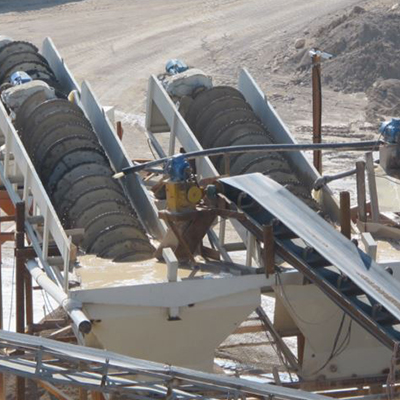
مانند بسیاری از ماشینآلات دیگر در تولید و فرآوری سنگدانه بتن، تصمیمگیری در مورد استفاده ساینده آبی و شوینده الواری یا هر دو، تا حد زیادی وابسته به مشخصات توده است. متصدیان امر گاهی اوقات چندین دوره آزمایشی را جهت تعیین تجهیزاتی که به بهترین نحو نیازهای آنها را برآورده سازد و عملیات را بهینه نماید، سپری میکنند.
اگر خواص توده به گونهای باشد که با این عملیات کاملاً شسته شود و مواد زیانآور به درصد اندک قابل قبولی کاهش یابد، متصدیان امر حقیقتاً خوششانس بودهاند و نیازی به استفاده از تجهیزات فرآوری پیچیده و گران نظیر جیکها (jik) یا جداسازیی به کمک مایعات سنگین نیست.
طبقهبندی هیدرولیکی ماسه
در اکثر مواقع جهت تهیه ماسهای با این دانهبندی که ذرات ریزتر از الک شماره ۲۰۰ آن در محدوده مجاز باشد، به طبقهبندی هیدروایکی ماسه نیاز است. بسیاری از تولیدکنندگان در روش تولید و فرآوری سنگدانه بتن،ماسه، بخش ریزتر ماسه شسته را برای ساخت ملات و اندود ذخیره میکنند.
دستگاههای طبقهبندی هیدرولیکی بر اساس این اصل مهم کار میکنند که ذرات درشتتر نسبت به ذرات ریزتر در محلول معلق آب، زودتر سقوط میکنند. با این فرض غیرحقیقی که ذرات کروی شکل در محیط لزج آزادانه سقوط میکنند، طبق قانون استوک، سرعت سقوط با مجذور شعاع ذرات متناسب است.
دستگاههای طبقهبندی ماسه تقریباً این شرایط ایدهآل را به کمک انواع دستگاهها با جریان افقی و بالارونده، نظیر حلزونیها، کششیها، شنکشها، چرخندهها و سیکلونها فراهم میکنند. چنانچه ذرات ماسه معلق در آب در یک انتهای مخزن یا کانال افقی طویل باشند و آب از انتهای دیگر سَرریز کند، حین حرکت آرام آب به سمت انتها (سرریز)، ذرات ریزتری رسوب خواهند کرد.
اگر کانال طولانیتر شود یا سرعت جریان آب کاهش یابد، به لحاظ افزایش زمان تعلیق، حتی ذرات نیز در انتهای مسیر رسوب میکنند. با فرض عدم آشفتگی جریان، همین اصول در دستگاههای طبقهبندیکننده با جریان بالارونده که اندازههای ریزتر ذرات به ارتفاعهای بالاتر حوضچه میروند، صادق است.
دستگاههای موجود در بازار از اصول فوق به روشهای مختلفی استفاده میکنند. دبی آبی که از سرریز انتهای تحتانی طبقهبندیکننده حلزونی میریزد، میزان ریزدانههای مانده را کنترل میکند. چرخش آرام حلزونی، ماسه را از داخل حوضچه بالا آورده و خشک میکند. کنترل این عملیات به ظاهر ساده برای تهیه ریزدانههای مورد نیاز، ضروری است.
برخی تولیدکنندگان که ریزدانه توده معدنی آنها در حال اتمام است یا مقدار زیادی آب نظیر آنچه از لایروبی حاصل میشود برای طبقهبندی ماسه استفاده میکنند، تمایل به کاهش ریزدانه دارند و لذا ممکن است در تأمین ۱۰ تا ۳۰% ذرات عبوری از الک نمره ۵۰ (ناحیه مجاز) با مشکل مواجه شوند.
شنشکنها اصولاً همان هدف حلزونیها را دنبال میکنند، لیکن رشته زنجیری همراه با تیغههای متصل به آن جایگزین حلزونی شده که ماسه را به سمت بالای بدنه شیبدار مخزن هدایت میکند.
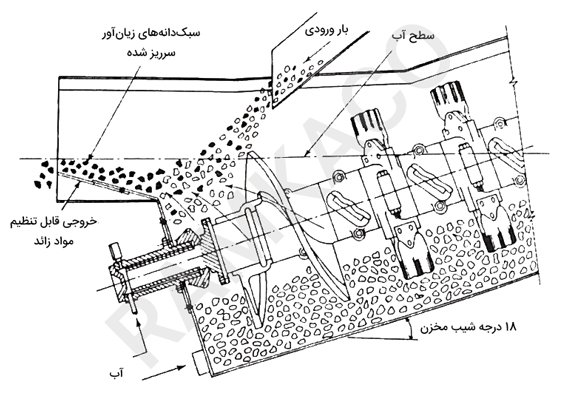
طبقهبندیکنندههای تجاری ماسه از اصول کانالهای طویل افقی استفاده میکنند؛ با این تفاوت که ۹ عدد سیلو در کف کانال، ماسههای با اندازه مختلف که در طول مخزن رسوب میکنند را خارج میکند. پس با مخلوط کردن این اندازهها، دانهبندیهای مختلف ماسه قابل حصول است. مخلوط کردن با اختلاط زیرآبی و بازگرداندن مجدد مصالح به طبقهبندیکننده حلزونی یا شنکش صورت میپذیرد. چنانچه ریزدانه به روشی مشابه درشتدانه مخلوط شود، اندازههای مختلف به خوبی مخلوط نمیشوند.
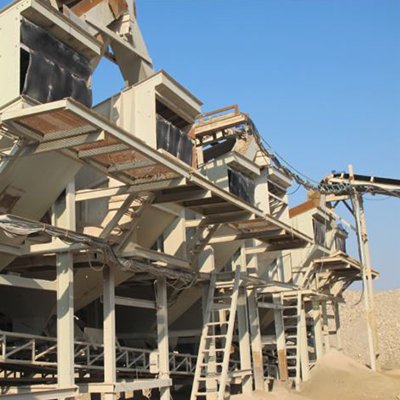
دستگاه دیگری که در فرآیند تولید ماسه بتن به کار میرود، سیلکون است. از این دستگاه هنگامی که به لحاظ حجم زیاد آب حاصل از لایروبی احتمال شسته شدن و از دست رفتن ریزدانهها وجود دارد، استفاده میشود. شکل زیر اصول کار سیکلون را نشان میدهد. حرکت چرخشی اعمالی به بار ورودی سبب حرکت ذرات درشتتر به سمت جداره بیرونی مخروط میگردد.
با تنظیم سه دبی جریان مربوط به لجن پمپ شده به داخل سیکلون، مواد بسیار ریز شده از قسمت فوقانی و در نهایت مقداری ریزدانه که در پایین بازیافت میشود، میتوان ریزدانههای بازیافت شده را مجدداً درون ماسه مخلوط کرد. گزارش شده که ذرات ریزتر از الک نمره ۵ به نحو مناسبی با سیکلون ۲۵۰mm و دبی لجن ورودی ۱۲۰۰lit/sec، به میزان ۱۰ton/h خشک و بازیافت شدهاند.
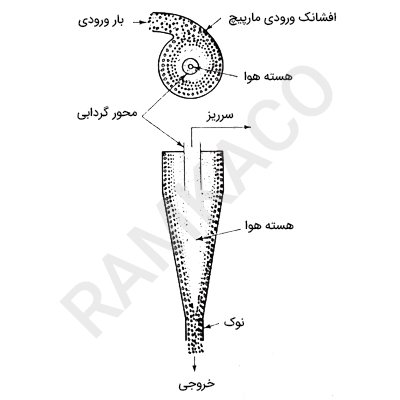
طبقهبندی خشک ماسه
در مناطق بسیار خشک که با کمبود آب مواجه هستند، دانهبندی خشک مواد ریز با استفاده از جداکنندههای هوایی صورت میپذیرد. ماسه تهیه شده از شکستن سنگ و ماسه روبارهای نیز گاهی اوقات به صورت خشک دانهبندی میشوند.
برخی جداکنندههای هوایی شبیه سیلکون کار میکنند؛ با این تفاوت که هوا به عنوان واسطه جایگزین آب میشود. این جداکنندهها اغلب به منظور زدودن مواد بسیار ریز ناشی از حملونقل یا گرد ناشی از شکستن مورد استفاده قرار میگیرند و مشابه طبقهبندیکنندههای سیلکونی در فرآیند تولید سیمان پرتلند کار میکنند.
در دستگاه دیگری، ماسه به وسیله پروانه گریز از مرکز به صورت افقی به خارج پرتاب میشود و در معرض جریان شدید هوای رو به پایین قرار میگیرد. نیروی گریز از مرکز، ذرات درشت را دورتر پرتاب میکند و لذا با توجه به اندازه ذرات، صفحات تقسیمکننده زیرین، ماسه منحرف شده را جمع میکند و عمل جداسازی بدین ترتیب انجام میشود.
از این لحاظ که به استثنای الک کردن آزمایشگاهی، در سایر وسایل دانهبندی جداسازی دقیقی انجام نمیشود (یا حقیقتاً ضرورتی نداره)، لذا مخلوط کردن پس از آن جهت جبران نقایص دانهبندی الزامی است.
مرحله پرعیارسازی
کاهش روزافزون منابع موجود سنگدانه، محدودیتهای منطقهای که از توسعه منابع مطلوب جدید جلوگیری میکند و سختگیری برخی سازمانها در مورد خصوصیات مورد نیاز سنگدانه، نیاز به توسعه و نصب تجهیزات ویژه جهت بالا بردن کیفیت سنگدانه ذخایر موجود یا بهبود منابع کشف شده که دارای سنگدانه با کیفیت پایین هستند را ایجاب میکند.
استفاده از بعضی ماشینآلات و تجهیزات پرعیارسازی، به جز در شرایط بسیار خاص مفید و مؤثر نبوده و بدین لحاظ روشهای جدیدی دائماً پیشنهاد و آزمایش میشوند. روشهای پرعیارسازی موجود، دو اصل اساسی را برای حذف مواد مضر به کار میبندند:
- جداسازی ثقلی
- ضربه با سایش مکانیکی، جهت خرد کردن قطعات نرمتر
جیگها و دستگاههای جداسازی به کمک مایعات سنگین، مواد مناسب را بر اساس چگالی از مواد نامطلوب جدا میکنند. قطعات نامناسب به وسیله آسیاهای قفسهای، آسیاهای غلتکی با آسترهای لاستیکی و بعضی اوقات، شویندههای الواری با ضربه یا سایش خرد میشوند. در هر مورد، روش پرعیارسازی با توجه به خواص توده تعیین میگردد.
بدیهی است چنانچه اکثر ذرات نامطلوب نرم باشند، روش پرعیارسازی ضربهای کافی خواهد بود. اگر ذرات زیانآور سخت و نرم هستند یا اینکه غالباً نظیر چرت، سخت اما چگالی آنها نسبتاً پایین باشن، میتوان از جیگ یا جداساز به کمک مایعات سنگین که گرانتر است، بهره گرفت.
آسیای قفسهای
سنگدانه وسط قفسه ریخته میشود و در اثر نیروی وزن از کف محفظه پایین میریزد. آسیاهای شبکهای دارای دو یا سه قفسه هممرکز که در جهت مخالف هم میچرخند، موجود هستند و لذا قادرند محصول را بیشتر خرد کنند.
آسیاهای قفسهای که با سرعت زیادی کار میکنند، جهت خرد کردن مورد استفاده قرار میگیرند و در این حال محصولِ بسیار مکعبیتری تولید میکنند. به هر حال بعضی متصدیان سرعت دوران را کم میکنند تا میزان خرد کردن را کاهش دهند، لیکن هنوز ضربه کافی جهت خرد کردن ذرات وجود دارد.
به منظور کاهش ابعاد سنگ نرم با قفسه به قطر ۰٫۹m، سرعت دوران ۶۰۰rpm بوده است. در بعضی تأسیسات، محصول آسیای قفسهای برای جداسازی قطعات خرد شده به شوینده الواری وارد میشود. به هر حال سنگ شکسته که ابعاد آن تا حد گرد و غبار کاهش یافته، بایستی با دستگاههای مناسب از محصول زدوده شود.
نظیر کلیه روشهای پرعیارسازی نمیتوان بر ضرورت مطالعه دقیق قبلی در مورد کارآیی آسیای قفسهای در بهبود محصول توده پیش از نصب تأسیسات، تأکید فراوان کرد. یکی از بهترین روشهای ممکن این است که یک یا دو کامیون بار را به نزدیکترین تأسیسات دارای آسیاب قفسهای حمل نمود و مقادیر معینی از آن را به منظور تعیین مزیتهای فرآیند در مقیاس عملیاتی واقعی بررسی کرد.
پرعیارسازی به وسیله جیگ
پرعیارسازی جیگ از اصول «تهنشینی تأخیری» در روش تولید و فرآوری سنگدانه بتن، بهره میگیرد که وقتی ذرات با چگالی مختلف در آب و در معرض نوسانات سریع عمودی قرار میگیرند، به نشست در لایههای افقی تمایل دارند. ذرات سنگینتر سریعتر از دانههای سبک (با چگالی کم) تهنشین میشوند.
اگر جربان آب جهتدار دائماً در محلول معلق تحت نوسان درون مخزن با کف شیبدار برقرار باشد، ذرات سنگین به سمت کف خروجی در انتهای مخزن حرکت کرده و ذرات سبک وزن همراه با آب از روی مانع سرریز میکنند. ارتفاع این مانع جهت بهینه نمودن فرآیند پرعیارسازی تنظیم میشود.
در شکل زیر تصویری از یک نوع جیگ دیده میشود. در این غربال، نوسانات به وسیله وزنه خارج از مرکز مکانیکی ایجاد میشوند و بخش تحتانی (صندوقه) با پوسته لاستیکی به مخزن شیبدار متصل میگردد. کف مخزن از صفحه فولادی سوراخداری تشکیل شده که سوراخهایش به وسیله مجموعهای از گلولههای فولادی مسدود میشود. گلولهها به منظور جلوگیری از سقوط دانهها به داخل صندوق استفاده میشوند و با این وجود انتقال نوسانات آب را به مخزن ممکن میسازند. در برخی جیگها نیروی مکانیکی به وسیله هوای مرتعش تأمین میگردد.
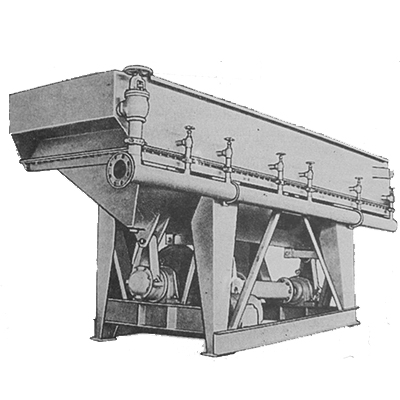
تنظیم دبی جریان آب، سرعت و وسعت عملیات غربال کردن، نرخ بار ورودی به جیگ و سرریز آب ضروری است و به منظور حصول فرآیند بهینه، بایستی با انجام آزمایشهایی تعادل دقیقی بین این موارد برقرار گردد. نرخ یکنواخت بار ورودی به جیگ، بایستی ضامن حفظ لرزش کامل کف باشد. ایجاد امواج روی آب با افت کارآیی همراه است. درباره تأثیر شکل و اندازه ذرات در کارآیی جیگ لرزهای، نظر واحدی وجود ندارد؛ اما هم درشتدانهها و هم ریزدانهها با این فرآیند غربال شدهاند.
پرعیارسازی با جیگ در مورد شنها که فاصله قابل ملاحظهای در چگالی دانههای مناسب و نامناسب وجود دارد، مؤثرترین روش است. برای نمونه ذرات چوب با چگالی اندک و شیل یا چرت با چگالی کمتر از ۲٫۳، از دانههای شن با چگالی بیش از ۲٫۶ جدا میشوند.
غربال کردن لرزهای موجب جداسازی وزنی کاملاً دقیقی نمیشود و بعضی دانههای سنگین همراه با سبکدانهها سرریز میشوند و به همین ترتیب، دانههای سبک محبوس شده و به داخل محصول خروجی راه پیدا میکنند.
جداسازی به کمک مایعات سنگین
در روش تولید و فرآوری سنگدانه بتن، جداسازی به کمک مایعات سنگین، علیرغم هزینه اولیه بالای آن (تقریباً پنچ برابر جیگ با ظرفیت مشابه) در مواردی که پرعیارسازی و جداسازی دقیق چگالی مشخص مورد نظر است، توسط اکثر تولیدکنندگان به کار میرود.
در این فرآیند، سنگدانه درون مخلوط معلق آب و ذرات ریز شده مگنتیت و فروسیلیکون وارد میشود. سنگدانههای با چگالی کمتر از مایع شناور میشوند و ذراتی که چگالی آنها از محیط محلول بیشتر است، تهنشین میگردند. هنگامی که چگالی مایع بین ۲ و ۳ مورد نظر است، نسبت مگنتیت به فروسیلیکون و رقیقسازی آب مخلوط، با دقتی برابر ۰٫۰۲ قابل تنظیم است. چگالیهایی که در عمل برای جداسازی شن به کار میرود، معمولاً در حدود ۲٫۴ تا ۲٫۶ است.
نمودار عملیاتی متداول در کارخانه جداسازی به کمک مایعات سنگین در شکل زیر مشهود است. جداسازی مواد رسوبی و شناور درون مخزن جداسازی انجام میشود. این مخزن تشت ثابت، استوانه گردان، پیش حلزونی یا مخروطی است. در مخزن نوع تشتی، مصالح تهنشین شده به وسیله پرهای با حرکات رفت و برگشتی از کف مخزن به سمت بالا جارو میشوند و مصالح شناور همراه با مایع که دائماً در حال گردش است، سرریز میشود.
نوع استوانهای مانند مخلوطکن ثابت بتن است و بالابرهایی داخل استوانه قرار دارند که مصالح تهنشین شده را هنگام چرخش استوانه از کف بالا آورده و روی ناوهای که به بیرون استوانه منتهی میشود میریزند. مصالح شناور همراه با مایع که دائماً در حال چرخش است، از لبه استوانه سرریز میشود.
نوع مارپیچی – حلزونی نظیر خشککن مارپیچی کار میکند، لیکن مایع سنگین جایگزین آب میگردد. مصالح شناور سرریز میشوند و شن تهنشین شده به کمک مارپیچ حلزونی از شیب بالا میآید. در نوع مخروطی از حوضچه عمیقی استفاده میشود تا جداسازی محصول تهنشین شده را که به وسیله هوا از رأس پایینی مخروط به مرکز آورده شده، انجام دهد. محاسنی برای هر یک از چهار نوع وسیله جداسازی عنوان میشود، اما کلیه آنها به صورت موفقیتآمیزی جهت پرعیارسازی شن یا ذرات ماسه درشت استفاده شدهاند.
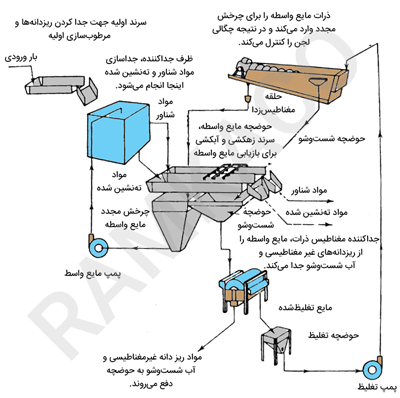
دیگر وسایلی که در شکل بالا دیده میشوند، به بازیابی مایع سنگین و بازگرداندن آن برای استفاده مجدد مربوط است. هم ذرات شناور و هم ذرات تهنشین شده هنگام خروج از دستگاه جداسازی با مواد چسبنده سیاه پوشیده شدهاند. برخی مواد مایع یکباره زهکشی میشوند و برای استفاده مجدد بازگردانده میشوند. مواد چسبنده مایع که به وسیله آبفشانها شسته میشود، به طریقه مغناطیسی بازیافت شده و توسط حلزونی خشککننده آبزدایی میگردد و سپس به منظور جلوگیری از به هم فشردگی آنها نامغناطیس میشوند.
هم مگنتیت و هم فروسیلیکون، دارای مغناطیسی هستند که کارخانه با فرآیند مناسب علیرغم ریزی آنها، کمترین مقدار این مواد را در آب شستوشو از دست میدهد. اتلافات مواد مایع بالغ بر ۳ تا ۴ سنت در هر تن محصول گزارش شده است. برآورده هزینه کل پرعیارسازی به کمک مایعات سنگین بین ۳۵ تا ۵۰ سنت در هر تن محصول است.
فرآیند جداسازی به کمک مایعات سنگین، سنگدانههای مضر را مستقیماً جدا نمیکند، اما مصالح را به خوبی بر اساس چگالی آنها به دو گروه با چگالی بیشتر از چگالی مایع و کمتر از چگالی مایع تقسیم میکند. اگر چگالی ذرات زیانآور کمتر از چگالی مایع باشد، به راحتی دفع میشود.
به ناچار قسمتی از سنگدانههای مناسب نیز که چگالی کمتری دارند، در فرآیند جداسازی هدر میروند. به همین ترتیب مصالحی با چگالی بیشتر، نظیر لیمونیت جدا نخواهد شد. با وجود اینکه این روش قادر به انجام جداسازی وزنی دقیق است، اما موفقیت آن به خواص توده و نوع ذراتی که باید برای تهیه محصول مناسب دفع شود، وابسته است. کارخانههای جداسازی به کمک مایعات سنگین موجود، ۲۰% بار ورودی را دفع میکنند.
دفع مواد زاید، مشکل عمده برخی تأسیسات فرآوری است، زیرا این مواد بایستی به صورت کامل از نواحی شهری خارج گردند. لذا معمولاً میتوان این مواد را به عنوان شن راهسازی، مصالح متخلخل خاکریز اطراف زهکشها و کاربردهای مشابه عرضه کرده و به فروش رساند.
در این مقاله از رامکا تلاش شد کلیه انواع روش مربوط به روش تولید و فرآوری سنگدانه بتن بررسی شده و اطلاعات جامعی در اختیار شما قرار گیرد. امیدواریم با مطالعه این مقاله توانسته باشید به تمام سؤالات خود در این زمینه پاسخ گویید. خواهشمندیم با ارائه نظرات خود در این زمینه، ما را در ارتقای کیفیت مقالات یاری رسانید.
درود و خسته نباشید بابت مقاله بلندبالایی که نوشته شده. گرچه خیلی بلند و طولانی هست. اما خب توضیحات جامعی را بیان کرده. سپاس بیکران از شما. 🌹🌹
سپاس از لطف شما🌹