بتن در سنین اولیه همانند نوزادی است که باید مراقبت شود تا به بلوغ برسد. عوامل زیادی در زمان تولید بتن در بچینگ، انتقال با میکسر، بتن ریزی، قالببرداری و عملآوری باید کنترل شوند تا در نهایت، بتن مطلوبی تولید شود. انتخاب صحیح مصالح و نسبتهای اختلاط، مهمترین گام برای دستیابی به بتنی با مقاومت در سازه است. برای رسیدن به این هدف، لازم است در سنین اولیه (دو روزگی بتن) توجه خاصی به بتن داشته باشید تا میزان کارایی، زمان گیرش، بلوغ و سرعت کسب مقاومت بتن کنترل گردد. در این مقاله از بلاگ رامکا، درصدد هستیم مراحل تولید بتن، بتن ریزی و عملآوری بتن را به همراه الزامات و شرایط آن در اختیار شما قرار دهیم. پس تا انتها همراه ما باشید.
بتن در سنین اولیه
همانطور که در دوران اولیه رشد کودک باید توجه ویژهای به او شود، بتن نیز در سنین اولیه خود نیازمند توجه ویژهای است؛ اما سؤال اینجاست که منظور از سنین اولیه بتن چیست؟ متخصصان بتن در مورد این نکته اتفاق نظر دارند که عوارض ناشی از افت کارایی در بتن تازه، هنگام بتن ریزی یا قبل از آن، جداشدگی دانهها، آبانداختگی هنگام متراکم شدن، روند کند کسب مقاومت، میتواند به طرز غیرمعمول بتن را دگرگون کند و از عمر مفید آن بکاهد.
مدت زمان مشخصی برای اندازهگیری سن اولیه وجود ندارد. برای رسیدن بتن به بلوغ مناسب، عوامل مختلفی چون: نوع سیمان، فعالیت سیمان، دما، انواع افزودنی بتن و… دخالت دارند. عموماً عامل زمان تعیینکننده نیست، مگر آنکه برای موردی، آن هم با احتیاط مشخص شود؛ البته در این میان، مقدار هیدراتاسیون عامل مشخصکننده بهتری است.
این اطلاعات در مواردی که کار جنبه عملی دارد، در دسترس نیست. یکی از تعاریف دیگر که بیشتر عملی است، زمان رسیدن بتن به خصوصیات مورد نظر است. تمام این زمانها سنین اولیه محسوب میشوند. به عبارت دیگر سنین اولیه، تابع روش مورد استفاده است. شخصی که وظیفه باز کردن قالبها را بر عهده دارد، این مدت را زمانی در نظر میگیرد که مقاومت بتن به ۱۵ مگاپاسکال برسد، حال آنکه شخصی که از قالب لغزنده استفاده میکند، نیاز به این میزان مقاومت ندارد. در این صورت، هیچ پاسخ جامعی برای سؤال مزبور وجود نخواهد داشت.
عدهای معتقدند هنگامی که نوع کار مشخص باشد، میتوان برای بتن معمولی در شرایط عادی، ۲۴ ساعت یا ۴۸ ساعت را معیار قرار داد، اما مقادیر گفته شده تقریبی هستند. از آنجا که مخلوط بتن معمولی (بتنی که با سیمان پرتلند معمولی ساخته شده و تحت عملیات بتن ریزی و دمای معمولی قرار میگیرد)، به ۶ تا ۱۰ ساعت زمان برای گیرش نیاز دارد و ۱ تا ۲ روز طول میکشد مقاومت مورد نظر را پیش از باز کردن قالب کسب کند، تعریف سن اولیه شامل مخلوط بتن با حالت خمیری و از سوی دیگر، شامل ۱ تا ۲ روز سن بتن سفت شده، بدون نیاز به مراقبت خاص میشود.
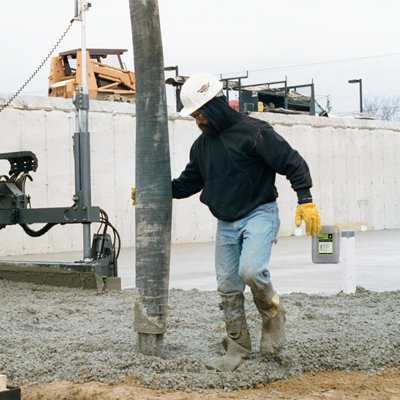
مدت زمان سن اولیه در مقایسه با طول عمر پیشبینی شده بتن بسیار کم است، اما در این مدت، عملیات بسیاری روی بتن صورت میگیرد که نهتنها تحتتأثیر خصوصیات مصالح قرار دارند، بلکه روی آنها نیز تأثیر میگذارند؛ به عنوان مثال، مخلوط بتن با کارایی کم به سختی مخلوط میشود و از سوی دیگر، اختلاط زیاد باعث کاهش کارایی میگردد. به طور کلی، ترتیب عملیات اصلی بتنریزی، مطابق آیتمهای ذیل است:
- پیمانه کردن بتن
- مخلوط کردن بتن
- انتقال مخلوط بتن از محل ساخت به کارگاه
- ریختن بتن شل یا خمیری در محل مورد نیاز
- متراکم کردن بتن
- پرداخت مخلوط بتن در زمانی که هنوز کارایی دارد.
- عملآوری برای دستیابی به مقاومت مورد نظر، پیش از قالببرداری
برای درک اهمیت عملیات و دستگاههای اصلی مورد استفاده، عملیاتی که در زیر شرح داده میشود، به چند بخش تقسیم میگردد. این عملیات در عمل با یکدیگر تداخل دارند؛ برای مثال، در روش کامیون و میکسر مخلوطکن، عملیات مخلوط کردن و حمل بتن به صورت همزمان انجام میشود.
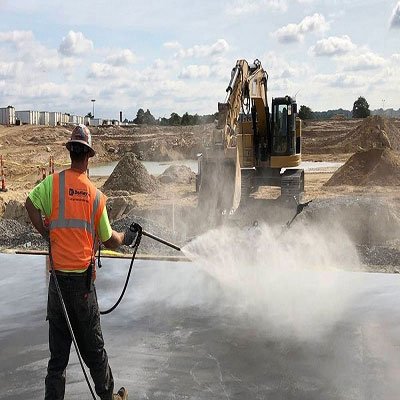
به طور کلی، بعضی رفتار بتن در سنین اولیه را نمیتوان به عنوان خصوصیات ذاتی مصالح در نظر گرفت، اما این رفتارها به دلیل تأثیری که در دراز مدت بر بازده سازه بتنی دارند، حائز اهمیتند. در عمل، بسیاری از این فرآیندها – چون: کارایی، میزان افت اسلامپ، جداشدگی دانهها و آبانداختگی، جمعشدگی خمیری، زمان گیرش دمای عملآوری – با یکدیگر ارتباط دارند، اما برای درک بهتر این خصوصیات و کنترل آنها، در ذیل هر یک به صورت مجزا مورد بررسی قرار میگیرند.
پیمانه کردن بتن (توزین)
اکثر توصیهنامههایی که در رابطه با پیمانه کردن مصالح بتن تدوین شده، بر اساس وزن مصالح ارائه شده است، نه حجم مصالح. این امر به دلیل تورم ماسه است که سبب بیدقتی در اندازهگیری میشود. آب و افزودنیهای محلول را میتوان به هر دو صورت وزنی یا حجمی و با دقت زیاد اندازهگیری نمود. امروزه در اکثر کشورها، پیمانه کردن و مخلوط کردن بتن در کارخانه، به صورت اتوماتیک یا نیمه اتوماتیک انجام میشود؛ برای مثال در ایالات متحده، در طول سالهای ۱۹۶۶ تا ۱۹۸۰، نسبت بتنهای ساخته شده با دست از ۵۴% به کمتر از ۲۵% رسید.
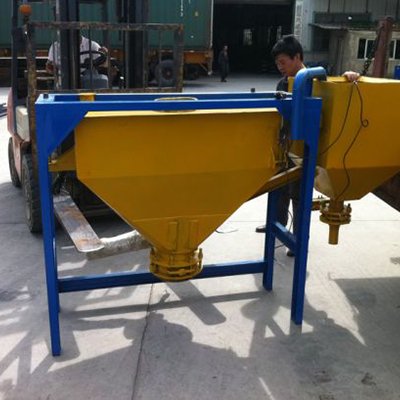
اختلاط بتن
خصوصیات ظاهری و فیزیکی بتن تازه، در صورت غیرمعقول بودن، به نامطلوب بودن روش اختلاط مرتبط است. بنابراین، مصالح بتن باید با نسبت دقیق و به طور مناسب و یکنواخت مخلوط گردند. امکان انجام عملیات مخلوط کردن در کارگاه یا در کارخانه نیز وجود دارد و این امر به مسائل اقتصادی، نوع اجرا و مقدار بتن مورد نیاز وابسته است.
در کارگاه میتوان از مخلوطکنهای سیار (جهت جادهسازی با روسازی بتنی) یا ساکن استفاده نمود. کارخانه بتن آماده، شامل مخلوطکنهای ثابت تا حجم ۹ متر مکعب است که میتواند از نوع کجشونده یا غیر کجشونده باشد. در نوع دیگر از مخلوطکنها، دریچه ورودی از بالا بوده و تعدادی تیغه نیز روی آن نصب شده است.
بتن آماده، یعنی بتنی که در مرحله خمیری و شل است و در کارخانه تحویل خریدار میگردد. در ۵۰ سال اخیر، صنعت بتن آماده پیشرفت زیادی داشته است؛ برای مثال، در ایالات متحده بیش از ۵۰۰۰ شرکت در حال استفاده از ۱۰۰۰۰ کارخانه هستند که بیش از دو سوم کل بتن مصرفی را تولید میکنند. اکثر کارخانهها، مجهز به سیستم پیمانه اتوماتیک یا نیمهاتوماتیک هستند و کنترل کارخانه توسط کامپیوترها و نرمافزارها انجام میشود. در ایالات متحده، معمولاً برای مخلوط کردن بتن، از کامیون مخلوطکن به جای مخلوطکن مرکزی استفاده میشود.
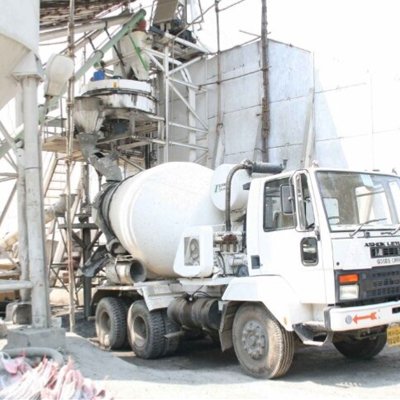
هر چند برای کنترل کیفیت بهتر، میزان استفاده از مخلوطکن مرکزی در سالهای بین ۱۹۶۶ تا ۱۹۷۷ از ۱۵% به ۲۷% افزایش یافته و میزان مخلوط کردن در کامیون از ۸۳% به ۷۱% کاهش یافته است. به طور معمول از مخلوطکن با دیگ چرخنده با محور مایل استفاده میشود که این نوع مخلوطکنها در دو نوع تخلیه از جلو یا تخلیه از عقب موجود هستند. در ۱۰ تا ۱۵ سال گذشته، برای کارهای مهم و بزرگ، تمایل از طرح اختلاط به روش نسبتها (۴ : ۲ : ۱)، به طرح اختلاط به روش مقاومت یا دوام تغییر یافته است. همچنین، مسئولیت کارخانههای بتن آماده در طرح اختلاط و کنترل کیفیت بیشتر شده است.
حمل و انتقال بتن
حمل بتن آماده به کارگاه، باید تا حد امکان سریع و پیش از سفتشدن بتن انجام پذیرد. در غیر این صورت، بتن ریزی، متراکم کردن بتن و پرداخت مطلوب آن با مشکل مواجه خواهد شد. بتن در مدت ۳۰ دقیقه، با سرعت کم یا به صورت متناوب مخلوط میشود و در طول زمان افت اسلامپ خواهد داشت، اما این فرآیند در مدت یک و نیم ساعت، مشکل جدی در بتنریزی و تراکم بتن محسوب نمیشود.
در چهل سال اخیر، در اصول حمل بتن با تسمه نقاله تغییرات بسیار کمی ایجاد شده است، ولی تغییرات عمدهای در تکنولوژی ساخت ماشینآلات رخ داده تا میزان بازده کار افزایش یابد. در این مدت، فرغون به فرغون مکانیکی تبدیل شده است. جام که با قرقره حمل می شد، به جرثقیل تبدیل شده و واگن حمل بتن، به کامیونهای بتن آماده (میکسرها) تغییر یافته است.
همچنین در عصر امروز، افزایش ارتفاع قالبهای بتنی و ضرورت انتقال قالبها، آرماتور و بتن به ارتفاع بالاتر، باعث پیشرفت در تکنولوژی جرثقیل شده و از جرثقیلهای برجی برای ساخت برجها استفاده میشود. در هر حال، مهمترین اصل در انتخاب روش و دستگاه حمل و ریختن بتن، این است که از جدا نشدن دانهها اطمینان حاصل شود.
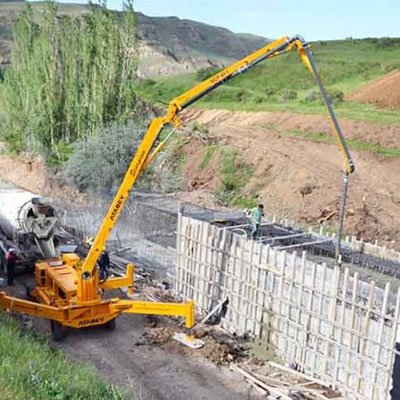
بیشتر بخوانید: مقاومت بتن
بتن ریزی
پس از ورود بتن آماده به کارگاه، بتن باید به نزدیکترین محل بتن ریزی منتقل شود. برای اینکه جداشدگی دانهها به حداقل برسد، در هنگام بتن ریزی در قالب یا دال، نباید آن را در مسافت طولانی حرکت داد. به طور کلی، بتن در لایههای افقی با ضخامت یکنواخت ریخته شده و هر لایه پیش از ریختن لایه بعدی، کاملاً متراکم میگردد.
سرعت بتن ریزی باید به حدی باشد که در هنگام بتن ریزی لایه جدید، لایه زیرین هنوز در حالت خمیری باشد. این کار مانع از به وجود آمدن درز اجرایی و صفحات ضعیفی که ناشی از ریختن بتن تازه روی بتن سفت شده است، میشود.
وسایل | محدوده کار و بهترین وسایل کاربرد | مزایا | نکاتی که باید دقت شود |
* کامیون با سرعت اختلاط کم | برای حمل بتن برای تمام کارهای جادهسازی، سازهها و ساختمانها، مسافت حمل باید به صورتی باشد که بتن در مدت یک و نیم ساعت تخلیه شود. البته این محدودیت قابل تغییر است. | کامیون با سرعت اختلاط کم، معمولاً برای حمل بتن از کارخانهای که کنترل کیفیت تولید بتن در آن رعایت شده و همچنین، تخلیه بتن از کامیون کاملاً کنترل شده به کار میرود. در هنگام تخلیه، بتن یکنواخت و همگن خواهد بود. | زمان تحویل باید به وسیله سازماندهی کار مناسب باشد. افراد و وسایل کارگاه باید آماده باشند تا حجم زیاد بتن را جایگذاری کنند. |
* کامیون مخلوطکن | برای انتقال بتن در مسافت کم و زیاد استفاده میشود. مسافت حمل محدودیت ندارد. | نیازی به مخلوطکن مرکزی نبوده و فقط پیمانهکن مرکزی نیاز است، زیرا تمام مرحله اختلاط در کامیون انجام میشود. نحوه تخلیه کاملاً مانند کامیون با سرعت کم است. | کنترل کیفیت به خوبی مخلوطکن مرکزی نبوده و در هنگام تخلیه، لازم است آزمایش اسلامپ انجام شود. تحویل گرفتن بتن باید به دقت صورت گیرد. |
کامیون غیر همزننده حمل بتن | برای حمل بتن در مقادیر کم مناسب است. | هزینه حمل بتن از روش کامیون با سرعت کم استوانه یا کامیون مخلوطکن کمتر است. | اسلامپ بتن باید محدود شود. امکان جداشدگی دانهها وجود دارد. برای انتقال بتن در ارتفاع، به سطح شیبدار (رمپ) نیاز است. |
کامیون مخلوطکن مداوم حمل بتن | برای تولید مداوم بتن در کارگاه استفاده میشود. | با ترکیبی از سیستم حمل مصالح و مخلوطکن متحرک، نسبتهای اختلاط بتن بر اساس مقادیر تعیین شده به شکلی دقیق قابل اجرا است. یک نفر جهت انجام عملیات کافی است. | برای انجام عملیات بدون اشکال، باید دستگاه بر اساس برنامه منظم نگهداری شود. مصالح باید بر مبنای نسبتهای طرح اختلاط استفاده شود. |
جرثقیل | وسیلهای مناسب برای کار در سطح بالاتر از زمین | برای ساخت ساختمانهای قابی بتن آرمه بلند که میتواند بتن، آرماتور و قالبها را حمل و منتقل کند. | از آنجا که فقط دارای یک قلاب است، باید به نحوی برنامهریزی شود که تمام وقت مورد استفاده قرار گیرد. |
جامها | برای ساخت ساختمانها و سدها با استفاده از جرثقیل و کابل مناسب است. با تسمه نقاله، میتوان بتن را از محل تخلیه به قالبها یا محل بتنریزی هدایت کرد. | امکان حداکثر استفاده از جرثقیل و مسیر کابل وجود دارد. تخلیه به نحو مطلوبی انجام میپذیرد. در ظرفیتهای مختلف موجود است. | ظرفیت جامها باید به اندازهای انتخاب گردد که با پیمانه بتن و ظرفیت دستگاه بتنریزی سازگار باشد. تخلیه باید به دقت انجام شود. |
فرغونها و دامپرها | برای مسافتهای کوتاه و هموار در کارگاههای ساختمانی مناسب است؛ بخصوص اگر جاده دسترسی محدودیت داشته باشد. | این روش بسیار انعطافپذیر است. بنابراین برای کارگاههایی که در آن شرایط بتنریزی متغیر است، مناسب میباشد. | کند است و نیاز به افراد زیادی دارد. |
شوتها | برای انتقال بتن به سطح پایینتر؛ به طور معمول برای زیر زمین در تمام کارگاههایی ساخت سازههای بتنی | هزینه کم و قابلیت مانور آسان نیازی به نیروی محرکه ندارد و نیروی ثقل تمام کار را انجام میدهد. | برای شیبهای ۱:۲ و ۱:۳، شوتها باید به طور مطلوب در تمام جهات مهار شوند. در انتهای شوت، باید لوله تخلیه وجود داشته باشد تا مانع از جداشدگی دانهها شود. |
تسمههای نقاله | برای انتقال بتن به طور افقی یا با ارتفاع بالاتر. معمولاً بین محل تخلیه و محل بتنریزی استفاده میشود. برای انتقال مستقیم بتن به قالبها مناسب نیست. | جهت هدایت تسمه نقاله قابل تنظیم بوده و با سرعتهای مختلف در جهات جلو و عقب قابل استفاده است. برای نقاطی که دسترسی مشکل است، بتن را با سرعت و در مقادیر زیاد منتقل میکنند. | در محل تخلیه، باید تمهیداتی اعمال گردد تا مانع از جداشدگی دانهها شود. روی تسمه بازگشت، نباید ملات باقی مانده باشد. در هوای نامطلوب (گرم، باد شدید)، مسیر طولانی تسمه باید پوشش داشته باشد. |
تفنگ بادی (لوله با نیروی باد) | برای مواردی که محل بتنریزی جای سختی قرار گرفته و مقطع بتن نازک و مساحت بزرگ است. | مناسب برای بتنریزی در قالبها با اشکال متفاوت، برای تعمیرات و تقویت ساختمانها. برای پوششهای حفاظتی و پوششهای بسیار نازک | کیفیت کار به مهارت افراد استفادهکننده از دستگاه بستگی دارد. فقط باید افراد ماهر به کار گرفته شوند. |
پمپهای بتن | برای انتقال مستقیم بتن از محل تخلیه مرکزی به داخل قالبها یا به محل بتنریزی | خطوط لوله فضای کمی را اشغال کرده و طول آن، به آسانی قابل ازدیاد است. انتقال بتن به طور مداوم امکانپذیر است. جرثقیل متحرک قادر است بتن را در جهات افقی و قائم هدایت کند. | تأمین میزان ثابت بتن تازه و خمیری، نیاز به روانی مناسب بدون ایجاد جداشدگی دانهها دارد. در هنگام پمپاژ بتن باید دقت نمود تا جریان بتن در خط لوله یکنواخت باشد. در پایان عملیات، لولهها باید کاملاً تمیز شوند. پمپاژ قائم و خمهای متعدد باعث کاهش مسافت پمپاژ میگردد. |
شوتهای بتنریزی قائم | برای جای دادن بتن در قالبهای قائم، بعضی از شوتها یک تکه هستند، ولی بعضی از آنها از چند قسمت قابل مونتاژ تشکیل شدهاند. | شوتهای بتنریزی قائم، بتن را به داخل هدایت کرده و آن را به پایین قالب انتقال میدهد؛ بدون آنکه جداشدگی دانهها در آن به وجود آید. استفاده از این شوتها باعث میشود خمیر سیمان و بتن روی قالبها تراوش نکند، زیرا در غیر این صورت، پس از قالببرداری، سطح بتن مطابق مشخصات تعیین شده نخواهد بود. آنها از جدا شدن دانههای درشت نیز جلوگیری میکنند. | شوتهای بتنریزی قائم باید به اندازه کافی بزرگ باشند. دهانه ورودی آنها باید مناسب و بزرگ باشد تا بتن بدون تراوش وارد آن شود. سطح مقطع آن باید به نحوی انتخاب گردد که امکان ورود به داخل قالب بدون تماس با آرماتور را داشته باشد. |
ترمی (قیف و لولهها) | برای بتنریزی زیر آب | برای انتقال به زیر آب، پیسازی یا هر قسمت دیگر سازه، میتواند مورد استفاده قرار گیرد. | باید دقت شود انتهای ترمی داخل بتن تازه قرار گیرد تا در نتیجه، حالت آببندی بین توده بتن و آب ایجاد شود. قطر آنها باید ۲۰۰ تا ۳۰۰ میلیمتر باشد، مگر اینکه تحت فشار قرار گیرد. پمپاژ بتن در آنها امکانپذیر است. مقدار سیمان مخلوط باید زیاد باشد (۳۶۳ تا ۴۴۶ کیلوگرم در متر مکعب) و به اسلامپ بالا (۱۵۰ تا ۲۳۰ میلیمتر) احتیاج است، زیرا بتن باید به صورت جاری باشد و به ویبره احتیاج نداشته باشد. |
بتن پخشکن | برای پخش بهتر روی سطوح صاف استفاده میشود. | با بتن پخشکن، مخلوطی که از جام یا کامیون تخلیه میشود، به سرعت روی سطوح وسیع و با ضخامت یکنواخت پخش میگردد. بتن پخش شده پیش از ویبره کردن برای تراکم نهایی، یکنواختی مناسبی دارد. | پخش بتن به عنوان بخشی از کار جادهسازی است که باید پیش از عمل ویبره اجرا شود. |
* به طور معمول استوانه کامیونهای بتن آماده، دو سرعت متفاوت دارند؛ کامیون با سرعت اختلاط کم، ۲ تا ۶ دور در دقیقه میچرخد و کامیون با سرعت اختلاط زیاد، بیش از ۶ دور در دقیقه میچرخد.
متراکم کردن و ویبره بتن
متراکم کردن بتن، مرحلهای است که باعث میشود بتن در قالبها و اطراف اجزای مدفون جای گیرد و مانع از ایجاد حبابهای هوا شود. این عمل را میتوان با یک میله نیز انجام داد، اما معمولاً از روشهای مکانیکی، مانند میله مکانیکی و ویبراتور استفاده میشود که جایگذاری مخلوط با نسبت آب به سیمان کم یا با مقدار شن زیاد را امکانپذیر میکند.
مخلوط بتن با روانی زیاد، باید به دقت متراکم گردد، زیرا تراکم باعث جداشدگی دانهها میشود. از ویبراتورها فقط باید برای متراکم کردن بتن استفاده نمود و برای انتقال بتن در جهت افقی از آنها استفاده نکرد، زیرا بکارگیری آنها موجب جداشدگی سنگدانهها میشود.
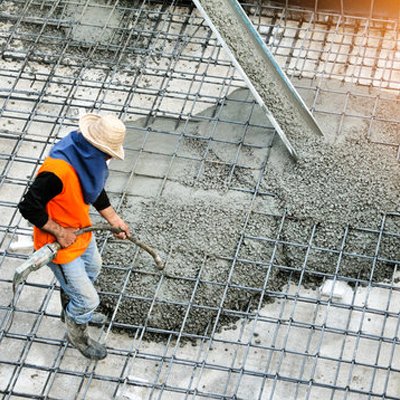
به طور کلی ویبره کردن به صورت داخلی یا خارجی، برای تراکم بتن استفاده میشود. در اثر ویبره کردن، اصطکاک میان ذرات سنگدانههای درشت (شن) به شدت کاهش مییابد. یکی از دلایل استفاده از ویبره داخلی، خروج حبابهای هوای داخل بتن است که با داخل کردن سریع ویبره به مخلوط و خارج کردن آهسته از مخلوط، همراه با بالا و پایین بردن ویبره انجام میشود. سرعت داخل شدن ویبره، باعث ایجاد نیرو در بتن شده و آن را به طرف بالا و بیرون حرکت داده و در نتیجه، هوای محبوس در بتن خارج میگردد. در هنگام بیرون آوردن ویبره از بتن، حبابهای هوا به سطح بتن منتقل میشوند.
- ویبرههای داخلی یا نفوذی: این ویبرهها که ویبرههای بیلچهای یا سیخی نیز نامیده میشوند، معمولترین وسیله برای تراکم بتن در تیرها، ستونها، دیوارها و دالها است. این ویبره، از یک سر استوانهای ارتعاشی به قطر ۱۹ تا ۱۷۵ میلیمتر تشکیل شده که توسط محور انعطافپذیر به موتور محرک متصل میشود. در سر ویبره، وزنهای با سرعت زیاد به صورت خارج از مرکز دوران میکند که باعث دوران سر ویبره در مداری دایرهای میشود.
ویبرههای کوچک، فرکانس بین ۱۰۰۰۰ تا ۱۵۰۰۰ دور در دقیقه داشته و دامنه آنها کوچک و بین تا ۰٫۴ تا ۰٫۸ میلیمتر (تغییر مکان از نقطه سکون) است. با افزایش قطر، فرکانس کاهش یافته و به دامنه اضافه میگردد. ترتیب عملیات مطلوب متراکم کردن بتن به وسیله ویبره با فرکانس زیاد، در شکل زیر نشان داده شده است.
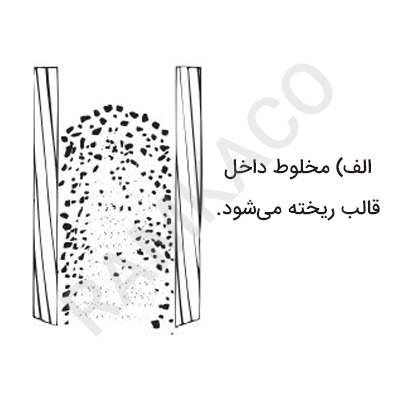
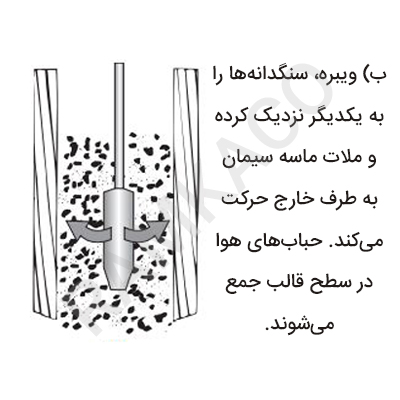
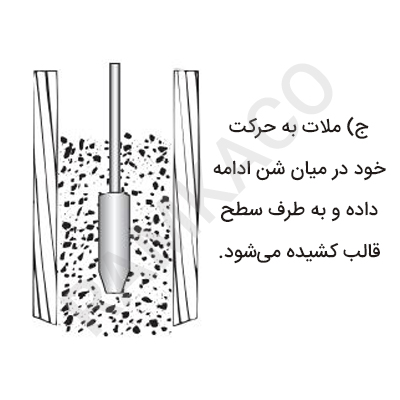
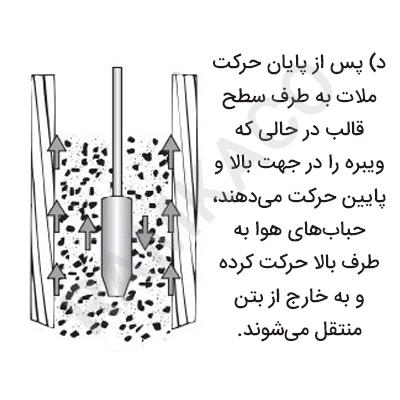
- ویبرههای خارجی یا ویبرههای قالب: این ویبرهها قابلیت نصب بر سطح بیرونی قالب را دارند و بیشتر بیشتر برای المانهای نازک یا پرفولاد استفاده میشوند. با استفاده از ویبره خارجی، برای قطعات پر آرماتور و تا وقتی که بتن هنوز شل باشد، حبابهای هوا و آب محبوس شده در زیر آرماتورها حرکت کرده و از بتن خارج شده و در نتیجه، مقاومت پیوستگی بین بتن و آرماتور افزایش مییابد. در صنایع قطعات پیشساخته، معمولاً از میز ویبره استفاده میشود. این میزها کنترل فرکانس و دامنه داشته و طبق اندازه قطعات و روانی بتن قابل تنظیم هستند. ویبرههای سطح مانند شمشه ویبره، برای متراکم کردن بتن کفها و دالها تا ضخامت ۱۵۰ میلیمتر مورد استفاده قرار میگیرند.
- ویبره مجدد بتن: این ویبره یک تا دو ساعت پس از مرحله تراکم اولیه، پیش از گیرش انجام میشود و گاهی اوقات برای اتصال لایههای بتن به یکدیگر به کار میرود. این عمل سبب حذف ترک، تخلخل یا ناحیه ضعیف ناشی از نشست یا آبانداختن، بخصوص در اطراف آرماتور با مصالح مدفون دیگر میشود.
برای سطوحی مانند دالها و جادهها، پرداخت مطلوب مورد نیاز است تا سطح کاملاً سفت شده و بدون احتیاج به تعمیر و نگهداری باقی بماند. در بعضی موارد، سطوح احتیاج به شمشهکاری و هموار کردن دارند، ولی در بسیاری از مواقع، عملیات پرداخت، شامل انجام عملیاتی است که باید با دقت و با در نظر گرفتن گیرش و سختشدن مخلوط بتن صورت گیرد.
بیشتر بخوانید: بتن مگر
پرداخت، شمشهکشی و مالهکشی بتن
شمشهکشی مرحلهای است که بتن مازاد را هموار کرده و سطح بتن را به ارتفاع مورد نظر میرساند. تیغه صاف با عمل ارهای خود در طول سطح حرکت کرده و بتن اضافی جلو تیغه جمعآوری شده و سطوح گود را پر میکند. ماله دسته بلند (تخته ماله دسته بلند)، بلافاصله پس از شمشهکشی استفاده میشود تا سنگدانههای درشت را در جای خود ثابت نگه داشته و سطح ناهموار باقی مانده را هموار سازد. مالهکشی باید پیش از آبانداختگی در سطح بتن به پایان رسد. در غیر این صورت باعث خرابی سطح، مانند خاکی شدن یا پوسته شدن دالهای بتنی میگردد.
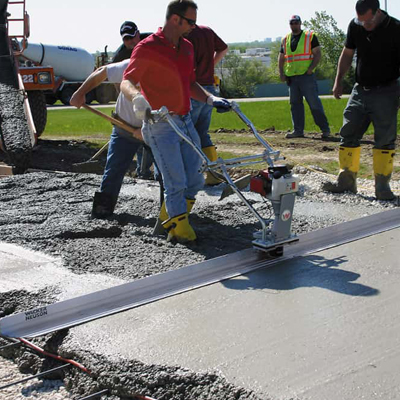
هنگامی که شبنم آبانداختگی تبخیر میشود و فشار پا جای کمی روی سطح بتن بر جای میگذارد، سطح آماده مالهکشی و عملیات پایانی پرداخت خواهد بود. عملیات نهایی مالهکشی با تیغههای صاف چوبی یا فلزی انجام میشود تا سنگدانهها محکم در جای خود باقی مانده، سطح کاملاً متراکم گشته و هر گونه ناهمواری بتن و اشکال در سطح بتن از میان برود.
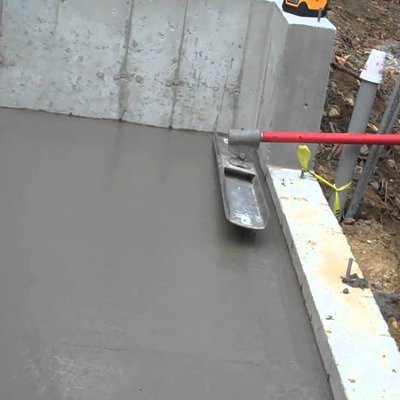
مالهکشی نهایی باعث میشود خمیر سیمان به طرف سطح حرکت کند. بنابراین مالهکشی خیلی زود یا خیلی دیر سبب ضعیف شدن سطح میشود. پس از مالهکشی، اگر سطح بسیار صاف و مقاوم در مقابل سایش مد نظر باشد، میتوان سطح را ماله فولادی کشید. ماله فلزی را نباید برای سطوحی که قبلاً مالهکشی نشده به کار برد. وقتی سطح مقاوم در مقابل لیز خوردن در نظر باشد، میتوان با جارو کردن یا خط انداختن با چنگک یا جارو با سیم فولادی، پیش از آنکه بتن به طور کامل سخت شود، جارو کرد (بتن باید تا حدی سخت شده باشد تا اثر خط روی آن باقی بماند).
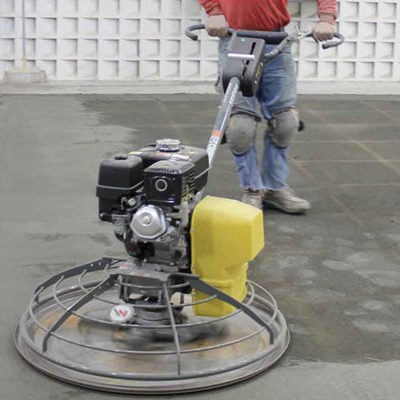
عملآوری بتن
دو هدف عملآوری، جلوگیری از افت رطوبت و کنترل دمای بتن برای مدت کافی، جهت دستیابی به حد مقاومت مورد نظر است. وقتی دمای محیط به اندازه کافی بالاتر از یخزدگی باشد، عملآوری دالها و جادهها میتواند با ساخت حوضچه روی آن یا غوطهور کردن آن انجام شود. دیگر سازهها میتوانند با آب فشاری، اسپری یا پوششهای اشباع شده با آب – مانند کتان یا گونی – عملآوری شوند.
این روشها باعث سرد شدن بتن از طریق تبخیر شده و برای بتنریزی در هوای گرم مناسب هستند. بخش دیگری از روشها، با جلوگیری از افت رطوبت بتن و بکارگیری ترکیبات عملآوری تشکیلدهنده غشاء، دمای بتن را ثابت نگاه میدارند. در مقابل، در بتن ریزی در هوای سرد وقتی دمای محیط کم است، بتن باید با استفاده از پتوهای عایقکننده از یخزدگی حفاظت شود. سرعت کسب مقاومت میتواند با عملآوری بتن به کمک بخار همراه با فشار، المنتهای حرارتی یا صفحات و قالبهای الکتریکی حرارتدهنده تسریع شود.
قالببرداری بتن
قالببرداری آخرین عملیاتی است که در سنین اولیه بتن انجام میشود. این عملیات مفهوم عمده اقتصادی را به همراه دارد، زیرا با اینکه قالببرداری سریع هزینههای ساخت را پایین میآورد، اما در بعضی سازههای بتنی، موجب فروپاشیده شدن ساختمانها میشود، زیرا هنوز بتن آنها به مقاومت کافی نرسیده است. از این رو تا زمانی که بتن برای تحمل تنشهای ناشی از هر دو بارهای مرده و حین ساخت، مقاومت کافی را کسب نکرده است، نباید قالبها را برداشت. همچنین هنگام قالببرداری، بتن باید به حد کافی سخت شده باشد تا سطح آن در هنگام برداشتن قالب یا فعالیتهای دیگر حین ساخت زخمی نشود.
از آنجا که مقاومت خمیر سیمان تازه هیدراته شده تابع دمای محیط و رطوبت مربوط است، بهتر است به جای یک زمان دلخواه منتخب، بر اندازهگیری مستقیم مقاومت بتن تکیه شود. برای قالببرداری تحت شرایط دمای استاندارد و عملآوری مرطوب، بتن معمولی ساخته شده با سیمان پرتلند نوع I در ۲۴ ساعت و بتنهای ساخته شده با سیمان نوع lll در ۱۲ ساعت، حد مقاومت مطلوب را کسب میکنند. برای ایمنی سازه در هوای سرد، طراحان حداقل مقاومت فشاری را پیش از آنکه بتن در معرض یخزدگی قرار گیرد، توصیه میکنند.
همانطور که گفته شد، بتن باید در سنین اولیه یا همان دو روزگیاش، تحت مراقبت شدید قرار گیرد تا به مقاومت و دوام مطلوب دست یابد. در این مقاله از بلاگ رامکا تلاش شد تمام مراحل بتن ریزی به طور کامل بررسی شود و الزامات لازم انجام گیرد. امیدواریم با مطالعه این مقاله توانسته باشید ۰ تا ۱۰۰ بتن ریزی را بیاموزید.
اشتراکها: بتن بدون جمع شدگی چیست؟ طرح اختلاط، خواص و کاربردهای بتن بدون ترک خوردگی
اشتراکها: دمای بتن؛ بهترین دما و زمان بتنریزی در فصل گرم و سرد سال | صنایع شیمی ساختمان رامکا
اشتراکها: افزودنی بتن در هوای سرد؛ بتنریزی در سرما و افزودنی زود گیر بتن | صنایع شیمی ساختمان رامکا